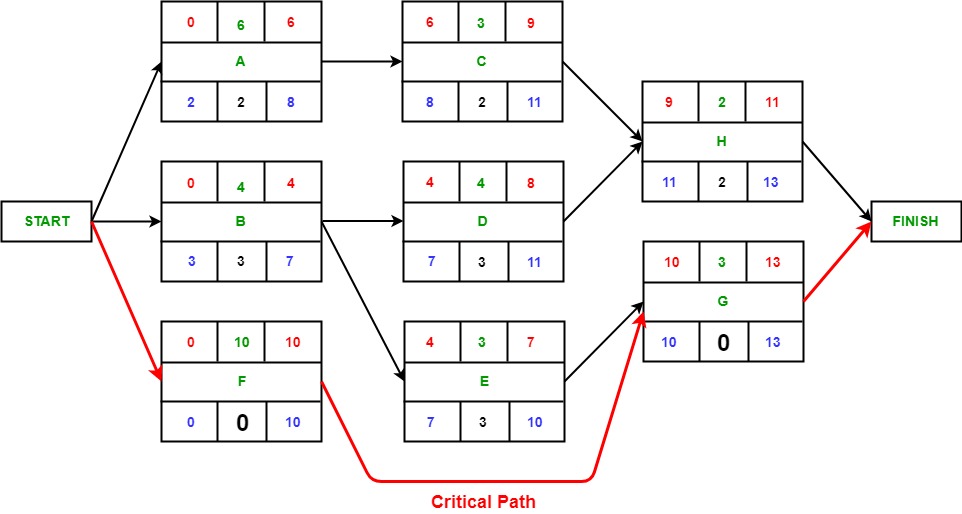
People going through transitions will likely experience four stages. These are: Rejection, Resistance and Exploration. And finally, Commitment. Each of these stages has its own set of challenges. It is important to know what you are trying to replace and keep. These will aid you during the transition.
Denialism
The four stages of change we experience are usually denial, acceptance, commitment and shock. The Stage of Shock, which is usually a short-term reaction, is the first. It causes a drop in productivity while the mind processes news and reality. This stage is known as the Stage of Denial and can last for quite a while. It is possible to lose touch and feel disconnected from reality if this stage is not overturned.
During this phase, people try to hold on to the current state of affairs and are trying to avoid facing the change. People may feel angry or sad as their energy fluctuates and performance is affected. It's essential to have effective support structures during this phase. If you are faced with the reality of change, it is important to be determined enough to make a move towards a new future.
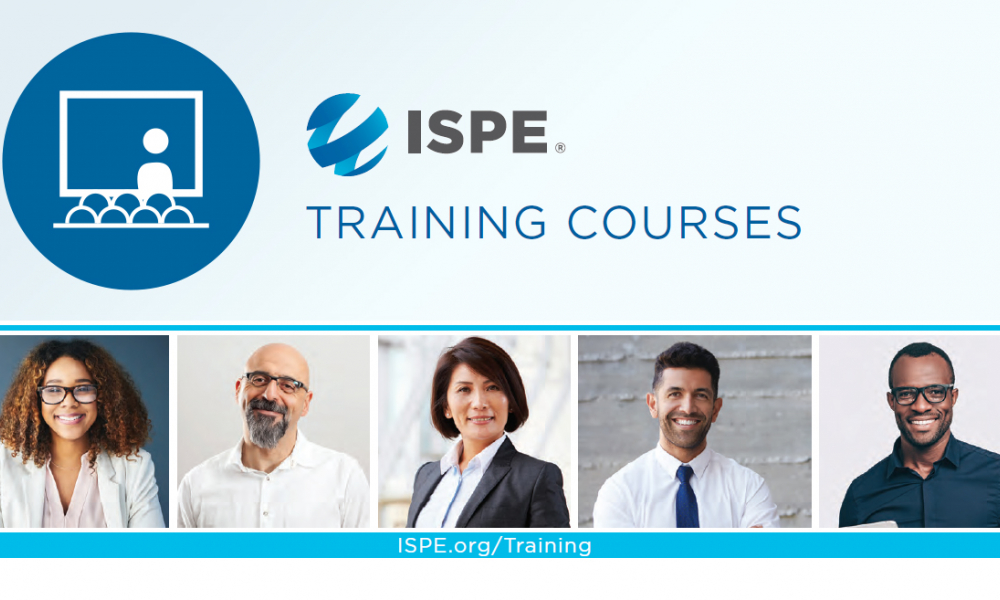
Resistance
An experiment was done to determine the effects of temperature on the resistance and strength of nickel alloys near their ferromagnetic phase transformation. The resistance to nickel at 25 and45 kbar was measured with a large hydrostatic cube multiple-anvil pressure device. This enabled the creation of a computerized, real time measurement system. The measurements revealed that the resistance measured at atmospheric temperature and at high pressures was in good agreement. The critical temperature, Tc, also increases with pressure at a rate between 0.193+ and 0.013 K/kbar.
These measurements revealed that phase transition resistance is due to the T-dependent gap function. This resistance stays constant at low temperatures. The resistance in the intergranular area increases if the temperature rises above the critical temperature. This feature is sensitive and shows that the resistive properties of the junction have been identified as SNS.
Exploration
The Exploration Phase of a transition is a critical time to build organizational capacity and learn more about the new program or practice. Participating in the implementation phase requires professionals and community stakeholders to be involved. This phase focuses on identifying the requirements of the program or practice, and then developing solutions to meet those needs. The Exploration Phase is where you identify the most important components and define the scope of the transition.
A team called the Implementation Team is responsible for creating, scaling up, and maintaining usable innovations. These teams combine drivers, stages, improvement cycles, and drivers into one holistic process. The process could begin with one person who brings new ways of working to the organization. However, it may also involve the creation of a team, which can be a key element in the sustainability process.
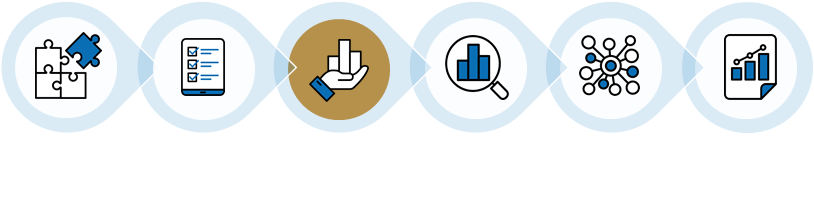
Engagement
Commitment to a change initiative is often accompanied by several phases. These phases are characterised by a lack in skills and setting, as well as a limited capacity to implement the changes. These phases will pass and people will either move to a new stage or continue in the current situation. However, once committed to a change initiative, individuals will be more likely to make progress.
The first phase of commitment is the Contact Stage. The Contact Stage allows employees to be exposed to the new initiative. This exposure may be in the form of a poor financial statement, a meeting with the CEO, or a meeting with senior staff.
FAQ
What is a basic management tool used in decision-making?
A decision matrix, a simple yet powerful tool for managers to make decisions, is the best. It allows them to think through all possible options.
A decision matrix is a way to organize alternatives into rows and columns. This makes it easy for you to see how each option affects other options.
In this example, we have four possible alternatives represented by the boxes on the left side of the matrix. Each box represents an option. The top row shows the status quo (the current situation), and the bottom row shows what would happen if nothing was done at all.
The effect of selecting Option 1 is shown in the middle column. In this example, it would lead to an increase in sales of between $2 million and $3 million.
The results of choosing Option 2 and 3 can be seen in the columns below. These are both positive changes that increase sales by $1million and $500,000. These changes can also have negative effects. Option 2 can increase costs by $100 million, while Option 3 can reduce profits by $200,000.
The last column shows you the results of Option 4. This will result in sales falling by $1,000,000
The best thing about a decision matrix is the fact that you don't have to remember which numbers go with what. You can just glance at the cells and see immediately if one given choice is better.
This is because the matrix has already taken care of the hard work for you. It's simply a matter of comparing the numbers in the relevant cells.
Here is an example of how a decision matrix might be used in your business.
It is up to you to decide whether to spend more money on advertising. If you do this, you will be able to increase revenue by $5000 per month. But, you will also incur additional expenses of $10 thousand per month.
You can calculate the net result of investing in advertising by looking at the cell directly below the one that says "Advertising." That number is $15 thousand. Advertising is a worthwhile investment because it has a higher return than the costs.
What is the difference between Six Sigma Six Sigma and TQM?
The key difference between the two quality management tools is that while six-sigma focuses its efforts on eliminating defects, total quality management (TQM), focuses more on improving processes and reducing cost.
Six Sigma stands for continuous improvement. This method emphasizes eliminating defects using statistical methods such p-charts, control charts, and Pareto analysis.
This method aims to reduce variation in product production. This is done by identifying root causes and rectifying them.
Total quality management includes monitoring and measuring all aspects of an organization's performance. It also includes the training of employees to improve performance.
It is often used to increase productivity.
What are the three basic management styles?
There are three main management styles: participative, laissez-faire and authoritarian. Each style has its own strengths and weaknesses. Which style do yo prefer? Why?
Authoritarian - The leader sets the direction and expects everyone to comply with it. This style works well if an organization is large and stable.
Laissez-faire: The leader lets each person decide for themselves. This style is best when the organization has a small but dynamic group.
Participative – Leaders are open to suggestions and ideas from everyone. This style is best for small organizations where everyone feels valued.
Six Sigma is so popular.
Six Sigma is easy and can deliver significant results. It provides a framework that allows for improvement and helps companies concentrate on what really matters.
Statistics
- The profession is expected to grow 7% by 2028, a bit faster than the national average. (wgu.edu)
- Hire the top business lawyers and save up to 60% on legal fees (upcounsel.com)
- The BLS says that financial services jobs like banking are expected to grow 4% by 2030, about as fast as the national average. (wgu.edu)
- As of 2020, personal bankers or tellers make an average of $32,620 per year, according to the BLS. (wgu.edu)
- This field is expected to grow about 7% by 2028, a bit faster than the national average for job growth. (wgu.edu)
External Links
How To
What is Lean Manufacturing?
Lean Manufacturing methods are used to reduce waste through structured processes. They were created by Toyota Motor Corporation in Japan in the 1980s. It was designed to produce high-quality products at lower prices while maintaining their quality. Lean manufacturing seeks to eliminate unnecessary steps and activities in the production process. It consists of five basic elements: pull systems, continuous improvement, just-in-time, kaizen (continuous change), and 5S. It is a system that produces only the product the customer requests without additional work. Continuous improvement is the continuous improvement of existing processes. Just-in time refers to components and materials being delivered right at the place they are needed. Kaizen refers to continuous improvement. It is achieved through small changes that are made continuously. The 5S acronym stands for sort in order, shine standardize and maintain. These five elements are used together to ensure the best possible results.
The Lean Production System
Six key concepts form the foundation of the lean production system:
-
Flow is about moving material and information as near as customers can.
-
Value stream mapping - Break down each stage in a process into distinct tasks and create an overview of the whole process.
-
Five S's: Sort, Shine Standardize, Sustain, Set In Order, Shine and Shine
-
Kanban – visual signals like colored tape, stickers or other visual cues are used to keep track inventory.
-
Theory of Constraints - Identify bottlenecks in the process, and eliminate them using lean tools such kanban boards.
-
Just-intime - Order components and materials at your location right on the spot.
-
Continuous improvement - Make incremental improvements rather than overhauling the entire process.