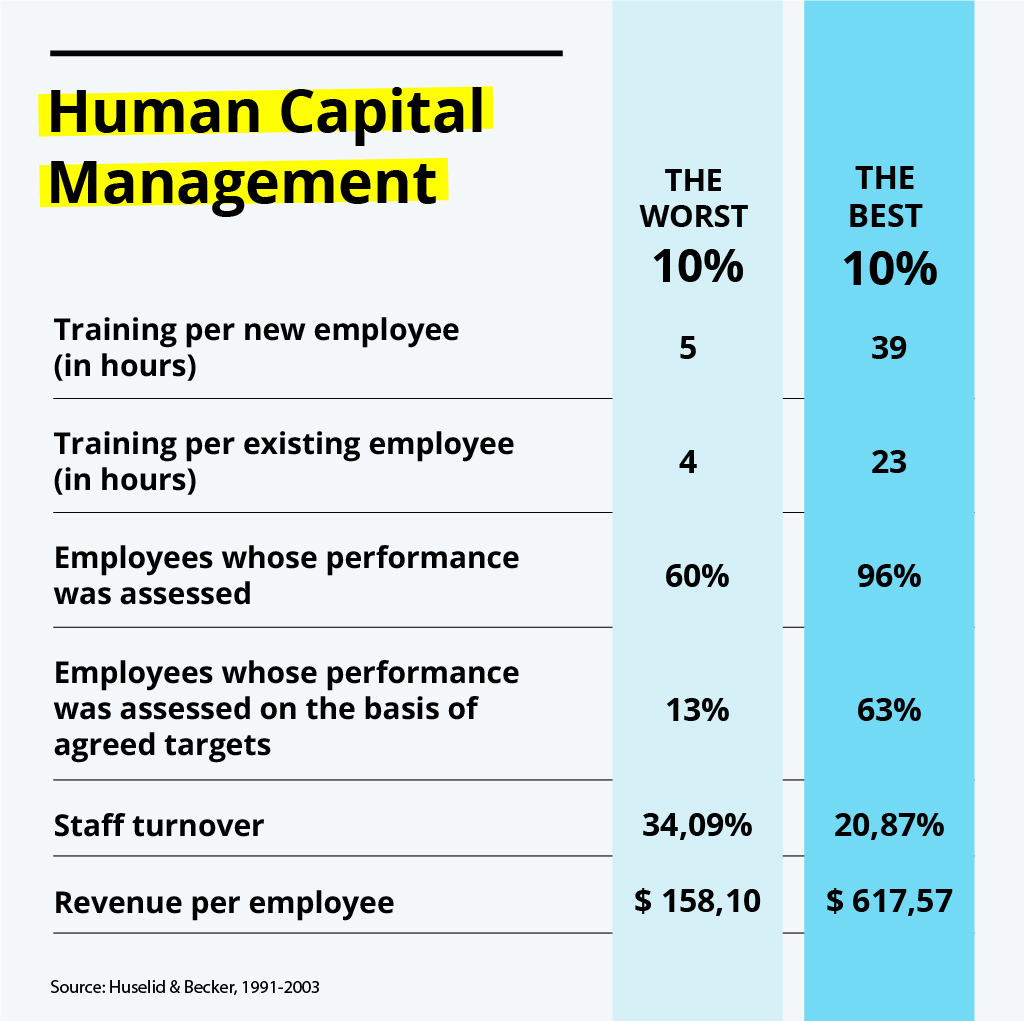
There are many things you can do if you have difficulty meeting deadlines. The first step is to create a detailed schedule. You must also understand the expectations of the client or employer. It is also important to avoid distractions. When you are clear about what you want, you can plan your time accordingly.
Setting clear expectations
It is important to set clear expectations for your team. This will help you engage them. Employees want to know that you expect them to be successful and that their work matters. Clear expectations can help you create unity and prevent bottlenecks by setting clear expectations.
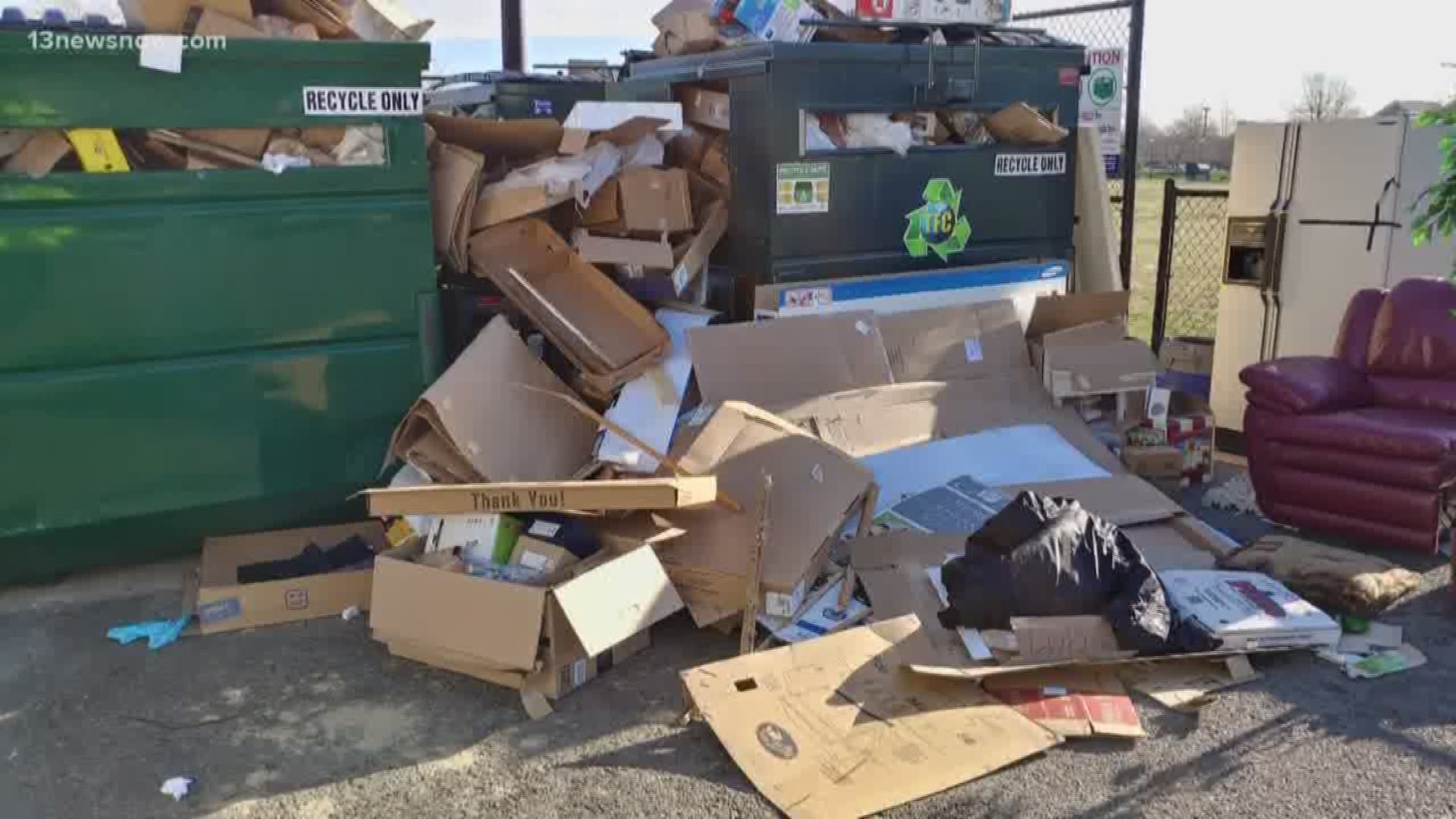
Alarms can be set up regularly
The first step in setting up an alarm is to choose the type. In many cases, you can choose an exact or an inexact repeating alarm, depending on the app you use. Inexact repeating alerts will not allow you meet specific deadlines but are less precise. They also reduce battery usage.
Avoiding distractions
For meeting deadlines, it's important to avoid distractions and identify them. Developing a clear schedule and setting priorities will help you focus on the tasks at hand and avoid being distracted by other things. Set time limits to ensure you have a clear schedule and are able to manage your time effectively. You should not switch your attention between tasks as it will lead to wasted time.
Monitoring progress
It is essential that you keep track of your progress in deadline-oriented tasks. This is best achieved by creating a checklist. The checklist should include brief descriptions of each task, as well its function. This will help you stay motivated and focused while you work. To help you distinguish between tasks, you can use a color-coded system.
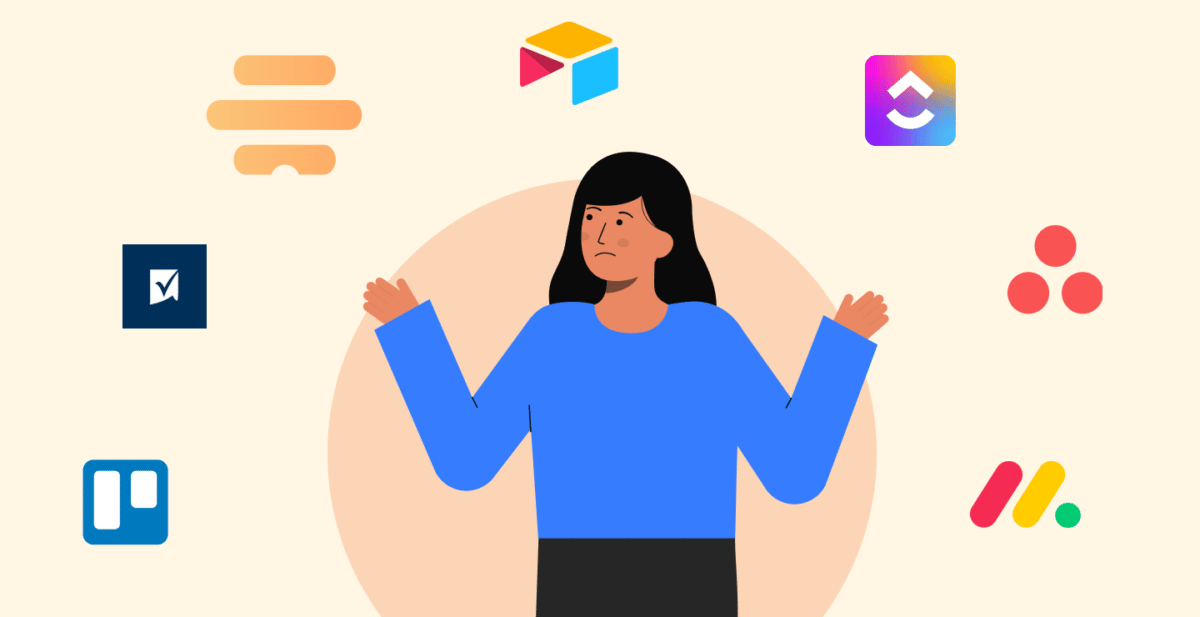
Making a Gantt diagram
Gantt charts are an excellent way of visualizing the project's timeline. You can adjust the chart to your requirements and the needs for your team. You can, for example, use different colors for different task bars to represent different members of your team, or assign different colors to different phases.
FAQ
What is TQM, exactly?
The industrial revolution led to the birth and growth of the quality movement. Manufacturing companies realized they couldn't compete solely on price. To remain competitive, they had to improve quality as well as efficiency.
Management developed Total Quality Management to address the need for improvement. It focused on all aspects of an organisation's performance. It included continuous improvement, employee involvement and customer satisfaction.
What is the difference in Six Sigma and TQM?
The main difference between these two quality management tools is that six sigma focuses on eliminating defects while total quality management (TQM) focuses on improving processes and reducing costs.
Six Sigma can be described as a strategy for continuous improvement. This method emphasizes eliminating defects using statistical methods such p-charts, control charts, and Pareto analysis.
This method has the goal to reduce variation of product output. This is done by identifying and correcting the root causes of problems.
Total quality management includes monitoring and measuring all aspects of an organization's performance. Training employees is also part of total quality management.
It is used to increase productivity.
What's the difference between a program and a project?
A project is temporary while a programme is permanent.
A project has usually a specified goal and a time limit.
It is usually done by a group that reports back to another person.
A program is usually defined by a set or goals.
It is usually implemented by a single person.
What is a basic management tool used in decision-making?
A decision matrix can be a simple, but effective tool to assist managers in making decisions. They can think about all options and make informed decisions.
A decision matrix is a way to organize alternatives into rows and columns. This allows one to see how each alternative impacts other options.
In this example, there are four possible options represented by boxes on the left-hand side of the matrix. Each box represents a different option. The top row depicts the current status quo, while the bottom row represents what would happen if no action was taken.
The middle column shows the effect of choosing Option 1. This would result in an increase of sales of $2 million to $3million.
The next two columns show the effects of choosing Options 2 and 3. These are both positive changes that increase sales by $1million and $500,000. These changes can also have negative effects. Option 2 increases costs by $100 thousand, while Option 3 decreases profits to $200 thousand.
The final column shows the results for Option 4. This results in a decrease of sales by $1,000,000
The best part of using a decision-matrix is that it doesn't require you to know which numbers belong where. The best thing about a decision matrix is that you can simply look at the cells, and immediately know whether one option is better or not.
This is because the matrix has done all the hard work. It's simply a matter of comparing the numbers in the relevant cells.
Here's an example of how you might use a decision matrix in your business.
Decide whether you want to invest more in advertising. By doing so, you can increase your revenue by $5 000 per month. But, you will also incur additional expenses of $10 thousand per month.
You can calculate the net result of investing in advertising by looking at the cell directly below the one that says "Advertising." That number is $15 thousand. Therefore, you should choose to invest in advertising since it is worth more than the cost involved.
Statistics
- As of 2020, personal bankers or tellers make an average of $32,620 per year, according to the BLS. (wgu.edu)
- This field is expected to grow about 7% by 2028, a bit faster than the national average for job growth. (wgu.edu)
- Hire the top business lawyers and save up to 60% on legal fees (upcounsel.com)
- Our program is 100% engineered for your success. (online.uc.edu)
- Your choice in Step 5 may very likely be the same or similar to the alternative you placed at the top of your list at the end of Step 4. (umassd.edu)
External Links
How To
How does Lean Manufacturing work?
Lean Manufacturing processes are used to reduce waste and improve efficiency through structured methods. These processes were created by Toyota Motor Corporation, Japan in the 1980s. The goal was to produce quality products at lower cost. Lean manufacturing emphasizes removing unnecessary steps from the production process. It includes five main elements: pull systems (continuous improvement), continuous improvement (just-in-time), kaizen (5S), and continuous change (continuous changes). Pull systems allow customers to get exactly what they want without having to do extra work. Continuous improvement is constantly improving upon existing processes. Just-in–time refers when components or materials are delivered immediately to their intended destination. Kaizen stands for continuous improvement. Kaizen can be described as a process of making small improvements continuously. The 5S acronym stands for sort in order, shine standardize and maintain. These five elements are combined to give you the best possible results.
Lean Production System
Six key concepts are the basis of lean production:
-
Flow: The goal is to move material and information as close as possible from customers.
-
Value stream mapping is the ability to divide a process into smaller tasks, and then create a flowchart that shows the entire process.
-
Five S’s - Sorted, In Order. Shine. Standardize. And Sustain.
-
Kanban - use visual signals such as colored tape, stickers, or other visual cues to keep track of inventory;
-
Theory of constraints - identify bottlenecks in the process and eliminate them using lean tools like kanban boards;
-
Just-intime - Order components and materials at your location right on the spot.
-
Continuous improvement - Make incremental improvements rather than overhauling the entire process.