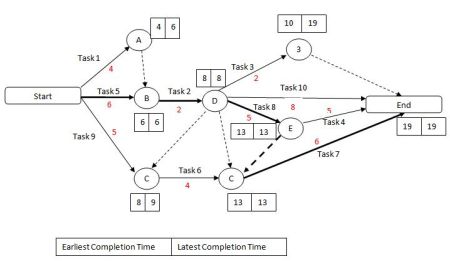
Definition of the role for middle management
The role of middle managers in a company's management is to bring together top-level executives with the employees below them. They convert the executive team's strategy into departmental goals. They collect data and provide results to their executive team. Their responsibilities range from making decisions on the allocation of resources to overseeing the work of subordinates.
In the federal government, middle managers have similar or greater supervisory roles than front-line supervisors. They are responsible for setting policies and guidelines to guide the work of employees at lower levels.
Middle managers face challenges
The conflicting roles of middle managers can lead to frustration. Managers have to manage subordinates and report to the higher-ups. However, they also have to enforce policies that aren’t theirs. Direct reports might object to these policies. Fortunately, technology can help middle managers cope with this dilemma. PwC, for instance, can identify digital training opportunities and direct managers to more that 300 courses.
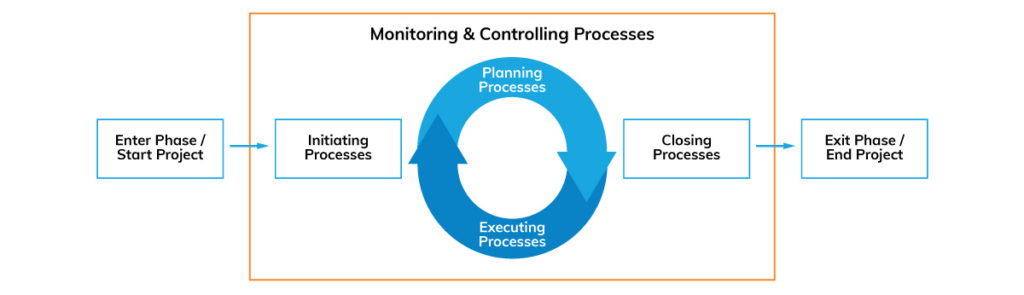
Middle managers should ensure that they have a good understanding of all involved parties and that they develop respect among them. This is not easy because their time may be constrained by multiple stakeholders. They must prioritize their tasks to ensure that they meet all requirements.
Tools to help middle managers collaborate
The role of middle managers is crucial in any organization. They have the responsibility of keeping track and moving information among teams and acting as a liaison between senior leaders and junior employees. Communicating with remote workers can be more difficult. There are many tools out there that will help middle managers collaborate better.
Many middle managers are required to attend a lot of meetings. This can consume up to 35%. Their time is limited and they don't have the ability to do any other work. A high cognitive load also results from video communication. This can lead to burnout.
Communication skills
Effective communication skills are vital to the success of middle managers. These professionals have a challenging role: they must work in close cooperation with both frontline employees and senior management, and they must deal with a constant cacophony of miscommunication and misunderstanding. The ability to communicate effectively can improve trust and engagement with colleagues, as well as their performance and influence.

Communication skills in middle management are essential in any field. In contrast to senior managers, middle managers can interact directly with employees. This means they need to be able and confident in communicating verbally and written. To avoid miscommunication and avoid mistakes, middle managers must be able to communicate clearly and effectively in writing.
FAQ
What is a basic management tool that can be used for decision-making?
A decision matrix is a simple but powerful tool for helping managers make decisions. It allows them to think through all possible options.
A decision matrix is a way of representing alternatives as rows and columns. This allows one to see how each alternative impacts other options.
This example shows four options, each represented by the boxes on either side of the matrix. Each box represents an option. The top row represents the current state of affairs, and the bottom row is indicative of what would happen in the event that nothing were done.
The middle column shows the effect of choosing Option 1. It would increase sales by $2 million to 3 million in this instance.
The results of choosing Option 2 and 3 can be seen in the columns below. These are both positive changes that increase sales by $1million and $500,000. But, they also have some negative consequences. Option 2 can increase costs by $100 million, while Option 3 can reduce profits by $200,000.
The final column shows the results for Option 4. This results in a decrease of sales by $1,000,000
The best thing about using a decision matrix is that you don't need to remember which numbers go where. Simply look at the cells to instantly determine if one choice is better than the other.
The matrix has already done all of the work. It's as easy as comparing numbers in the appropriate cells.
Here is an example of how a decision matrix might be used in your business.
Decide whether you want to invest more in advertising. If you do, you'll be able to increase your revenue by $5 thousand per month. You will still have to pay $10000 per month in additional expenses.
You can calculate the net result of investing in advertising by looking at the cell directly below the one that says "Advertising." That number is $15 thousand. Advertising is a worthwhile investment because it has a higher return than the costs.
What is Six Sigma?
Six Sigma uses statistical analyses to locate problems, measure them, analyze root cause, fix problems and learn from the experience.
The first step is to identify the problem.
Next, data is collected and analyzed to identify trends and patterns.
The problem is then rectified.
Finally, data is reanalyzed to determine whether the problem has been eliminated.
This cycle continues until the problem is solved.
What is Six Sigma?
It's an approach to quality improvement that emphasizes customer service and continuous learning. The goal is to eradicate defects through statistical techniques.
Motorola developed Six Sigma in 1986 to help improve its manufacturing processes.
The idea quickly spread in the industry. Many organizations today use six-sigma methods to improve product design and production, delivery and customer service.
What are the steps of the management decision-making process?
Managers are faced with complex and multifaceted decisions. It involves many elements, including analysis, strategy. planning. implementation. measurement. evaluation. feedback.
When managing people, the most important thing to remember is that they are just human beings like you and make mistakes. There is always room to improve, especially if your first priority is to yourself.
This video will explain how decision-making works in Management. We will explain the importance of different types decisions and how every manager can make them. The following topics will be covered.
What does it mean to say "project management"
We mean managing the activities involved in carrying out a project.
This includes defining the scope, identifying the requirements and preparing the budget. We also organize the project team, schedule the work, monitor progress, evaluate results, and close the project.
What are management principles?
Management concepts are the fundamental principles and practices that managers use when managing people and their resources. These include topics such as human resource policies and job descriptions, performance assessments, training programs and employee motivation.
What is Kaizen?
Kaizen, a Japanese term that means "continuous improvement," is a philosophy that encourages employees and other workers to continuously improve their work environment.
Kaizen is based on the belief that every person should be able to do his or her job well.
Statistics
- Your choice in Step 5 may very likely be the same or similar to the alternative you placed at the top of your list at the end of Step 4. (umassd.edu)
- 100% of the courses are offered online, and no campus visits are required — a big time-saver for you. (online.uc.edu)
- Our program is 100% engineered for your success. (online.uc.edu)
- This field is expected to grow about 7% by 2028, a bit faster than the national average for job growth. (wgu.edu)
- UpCounsel accepts only the top 5 percent of lawyers on its site. (upcounsel.com)
External Links
How To
What is Lean Manufacturing?
Lean Manufacturing techniques are used to reduce waste while increasing efficiency by using structured methods. They were created by Toyota Motor Corporation in Japan in the 1980s. The primary goal was to make products with lower costs and maintain high quality. Lean manufacturing is about eliminating redundant steps and activities from the manufacturing process. It includes five main elements: pull systems (continuous improvement), continuous improvement (just-in-time), kaizen (5S), and continuous change (continuous changes). It is a system that produces only the product the customer requests without additional work. Continuous improvement means continuously improving on existing processes. Just-in-time refers to when components and materials are delivered directly to the point where they are needed. Kaizen refers to continuous improvement. It is achieved through small changes that are made continuously. Five-S stands for sort. It is also the acronym for shine, standardize (standardize), and sustain. These five elements can be combined to achieve the best possible results.
Lean Production System
Six key concepts make up the lean manufacturing system.
-
Flow - focus on moving material and information as close to customers as possible;
-
Value stream mapping: This is a way to break down each stage into separate tasks and create a flowchart for the entire process.
-
Five S's – Sort, Put In Order Shine, Standardize and Sustain
-
Kanban - use visual signals such as colored tape, stickers, or other visual cues to keep track of inventory;
-
Theory of constraints - identify bottlenecks in the process and eliminate them using lean tools like kanban boards;
-
Just-in-time - deliver components and materials directly to the point of use;
-
Continuous improvement: Make incremental improvements to the process instead of overhauling it completely.