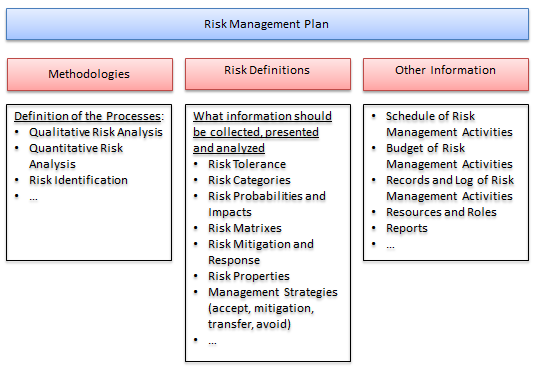
To submit your webinar ideas for consideration, please click here. Participating in CMAA webinars can be done for free. You will receive one CCM Renewal Point, one Professional Development Hour (PDH), and a certificate of completion. You can submit your idea for a construction-related webinar here.
Send us your idea to host a webinar on business of construction
There are many ways that you can promote your webinar. The best way is to make a landing site. It doesn't necessarily have to look fancy. A simple landing page is enough. Blog posts are also a good way to promote the webinar. The more people who know about your webinar, the more chances it will have to gain traction.
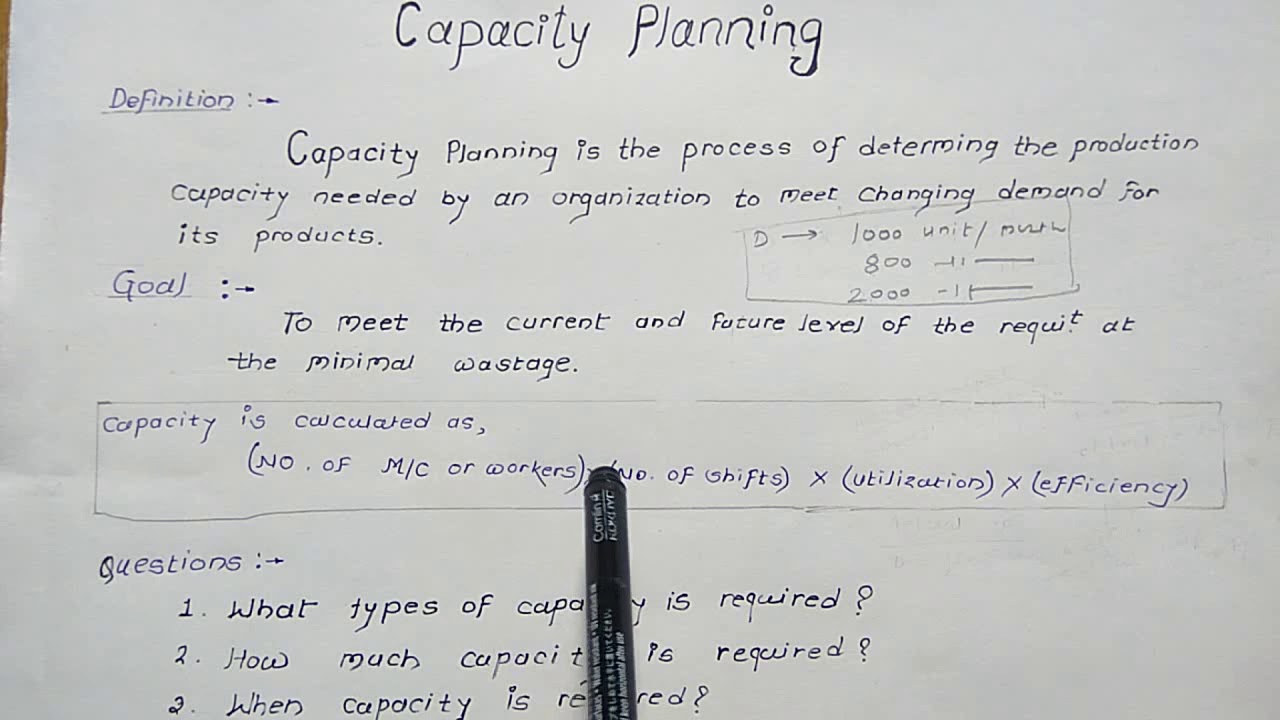
CMAA webinars offer 1 CCM Renewal Point (RP) and 1 Professional Development Hour (PDH)
CMAA webinars are available to CMs worldwide, and each offers 1 CCM Renewal Point (RP), or Professional Development Hour (PDH). PDHs and RMs are both valid for continuing education credits. Your CCM credential can be renewed by using RMs. The validity of the RMs is two years.
The CMAA Southern Nevada Chapter offers opportunities for professional development for construction managers. These include monthly breakfast meetings, educational activities, and CCM certification. Membership in CMAA National also offers professional education and training for construction managers. The professional development department is available to anyone who wants to update their knowledge or gain new insight.
Benefits of attending a webinar
A webinar can be a great way for you to increase your sales leads or improve customer service. A webinar is delivered in different formats, including a single speaker, panel discussions, or a moderator presenting multiple speakers. A successful webinar will have a strong message and stand out from the competition.
Webinars can easily be viewed from anywhere at any time. The presenter can prerecord the webinar and then post it at a convenient time. The entire experience is highly customizable. Webinars are accessible from all over the world, so participants can participate from anywhere.
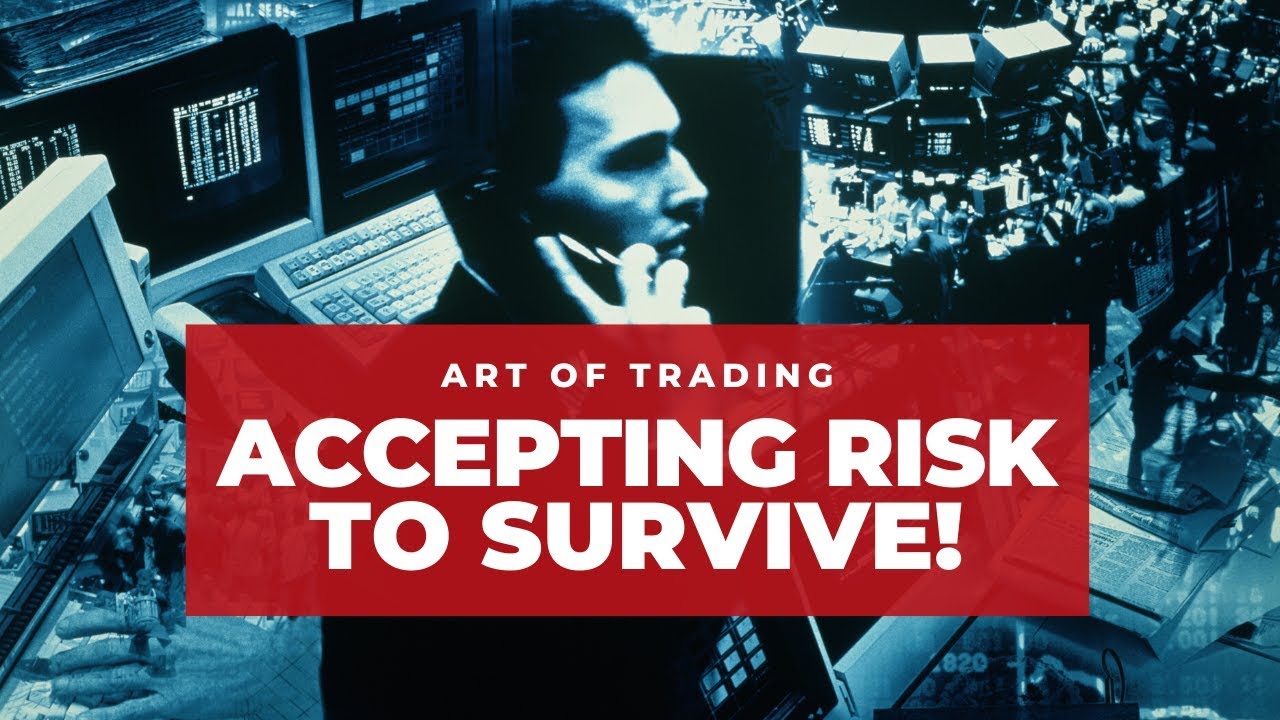
Webinars enable people to network and connect globally. They also allow participants to ask questions and provide feedback. A webinar can also provide a platform for thought leadership and training on current trends in the industry. Webinars allow you to reach a wide audience quickly and easily.
FAQ
What role can a manager fill in a company’s management?
The role of a manager varies from one industry to another.
A manager generally manages the day to-day operations in a company.
He/she will ensure that the company fulfills its financial obligations.
He/she ensures that employees follow the rules and regulations and adhere to quality standards.
He/she plans new products and services and oversees marketing campaigns.
What are the four main functions of management?
Management is responsible of planning, organizing, leading, and controlling people as well as resources. It includes creating policies and procedures, as well setting goals.
Management assists an organization in achieving its goals by providing direction, coordination and control, leadership, motivation, supervision and training, as well as evaluation.
Management's four main functions are:
Planning – Planning involves deciding what needs to happen.
Organizing - Organizing involves deciding how things should be done.
Directing - Directing is when you get people to do what you ask.
Controlling - Controlling means ensuring that people carry out tasks according to plan.
Why is it important that companies use project management methods?
Project management techniques ensure that projects run smoothly while meeting deadlines.
This is because many businesses depend heavily upon project work to produce products and services.
Companies must manage these projects effectively and efficiently.
Companies can lose time, money, and reputation if they don't have a good project management system.
Statistics
- This field is expected to grow about 7% by 2028, a bit faster than the national average for job growth. (wgu.edu)
- Hire the top business lawyers and save up to 60% on legal fees (upcounsel.com)
- UpCounsel accepts only the top 5 percent of lawyers on its site. (upcounsel.com)
- 100% of the courses are offered online, and no campus visits are required — a big time-saver for you. (online.uc.edu)
- Our program is 100% engineered for your success. (online.uc.edu)
External Links
How To
How can Lean Manufacturing be done?
Lean Manufacturing methods are used to reduce waste through structured processes. They were created by Toyota Motor Corporation in Japan in the 1980s. It was designed to produce high-quality products at lower prices while maintaining their quality. Lean manufacturing seeks to eliminate unnecessary steps and activities in the production process. It is composed of five fundamental elements: continuous improvement; pull systems, continuous improvements, just-in–time, kaizen, continuous change, and 5S. Pull systems involve producing only what the customer wants without any extra work. Continuous improvement refers to continuously improving existing processes. Just-intime refers the time components and materials arrive at the exact place where they are needed. Kaizen stands for continuous improvement. Kaizen can be described as a process of making small improvements continuously. Finally, 5S stands for sort, set in order, shine, standardize, and sustain. These five elements can be combined to achieve the best possible results.
Lean Production System
Six key concepts underlie the lean production system.
-
Flow - focuses on moving information and materials as close to customers as possible.
-
Value stream mapping - break down each stage of a process into discrete tasks and create a flowchart of the entire process;
-
Five S's: Sort, Shine Standardize, Sustain, Set In Order, Shine and Shine
-
Kanban: Use visual signals such stickers, colored tape, or any other visual cues, to keep track your inventory.
-
Theory of Constraints - Identify bottlenecks in the process, and eliminate them using lean tools such kanban boards.
-
Just-intime - Order components and materials at your location right on the spot.
-
Continuous improvement - Make incremental improvements rather than overhauling the entire process.