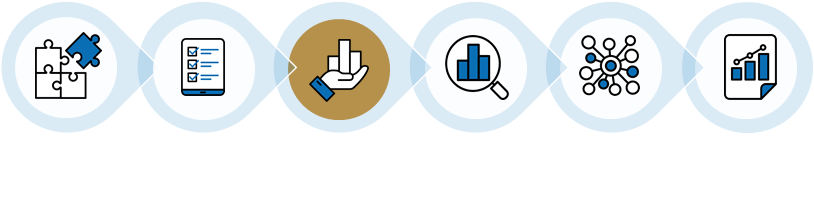
The five core principles of project management must be followed by every manager. These principles are Transparency (measurement), Trust (formalized structure) and Trust (trust). You can create a project which meets your goals, and your team's performance will improve by using these principles. These principles will ensure that your project is a success. What does each of these mean? Let's take a closer look. Let's start by asking what a standard for engagement is. It's the reference for the workforce who will be working on your project. Employees feel more responsible when there is a defined hierarchy.
Transparency
Transparency in project management can have a major benefit. It encourages teamwork. When everyone can access and share information, it is easier to collaborate and perform better. Transparency improves teamwork because members feel that they can trust one another. When information is shared openly, team members will be more likely to lend their help and offer valuable insights. This can improve productivity and make a project more successful.
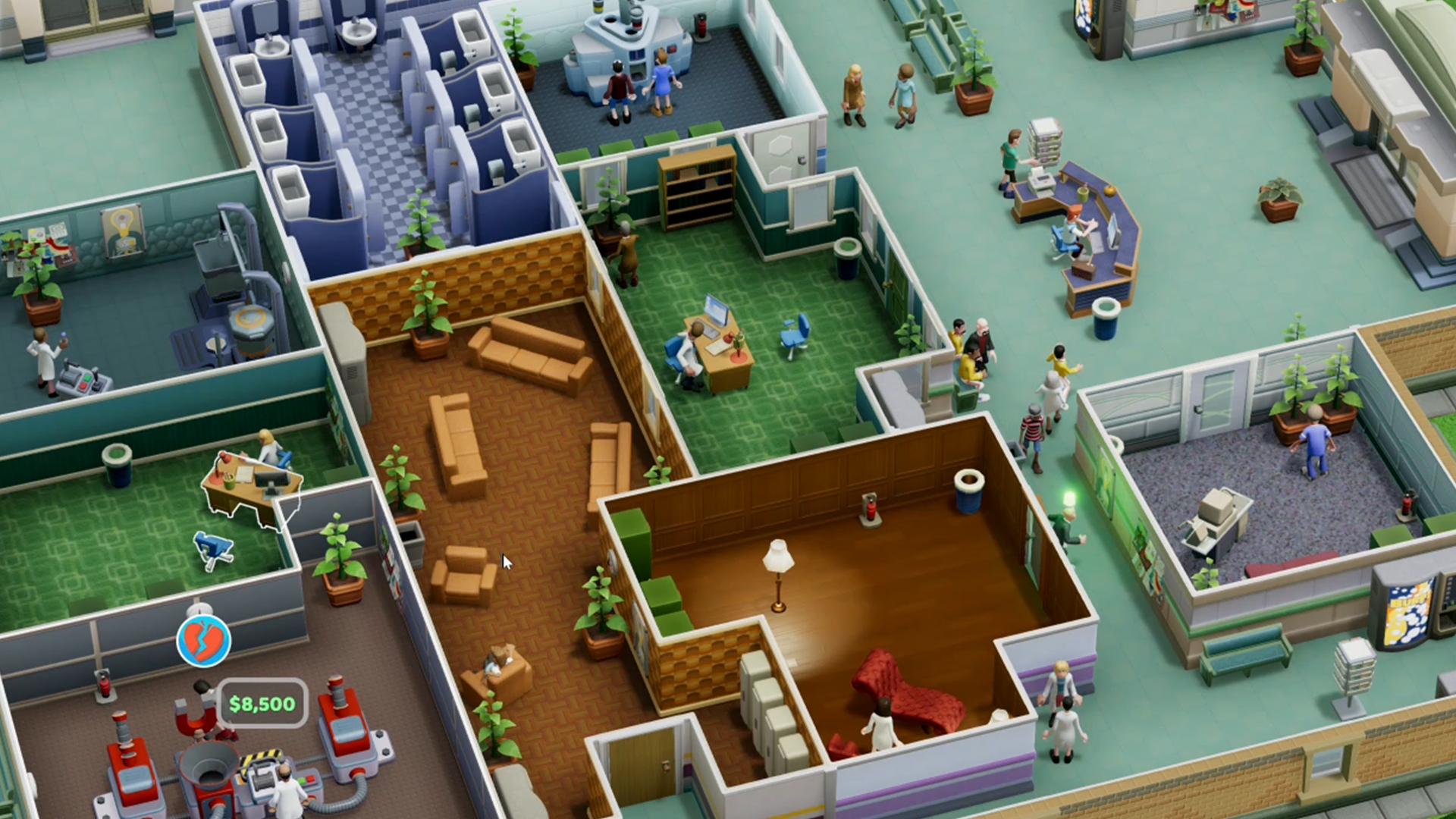
Trust
Project management is only possible if there are high levels of trust between members of the team. People who have trust in one another will be more productive and will be more inclined to delegate. They will also be more inclined to share information and ideas. Trust will also foster collaboration and speed up work. Trusting members of your team will also have other benefits, such as better communication, easier delegations, and faster decision making.
Measurement
There are 3 main measurement principles in project management. We first measure outputs against the baseline data and target outcomes. Second, we measure the project's performance against its objectives. The effectiveness of our methods is then measured. We then measure the overall success of the project in terms its outcomes. These principles will ensure that your projects are successful. Successful projects will be a benefit to both your company's and your customers.
Formalized structure
Using a formalized structure in project management can help your company improve its productivity and reduce the time it takes to bring new products to market. This can reduce engineering and manufacturing costs, which in turn can lower costs. Your organization can become more efficient at managing projects and increase your managerial skills by using formalized structures. This article will tell you why you should use formal structures for your projects. This will allow you to get the most from your projects.
Organisational alignment
This paper examines the literature on alignment and performance and identifies the different types. It also proposes research issues that will aid in the theory and practice management of alignment. Both horizontal and vertical alignment have been discussed in literature. However, the emphasis on vertical alignment has been greater than that on horizontal alignment. This shows there is much more to be done. This is because the effectiveness and commitment of the leadership team to the project's goals will determine the level of alignment.
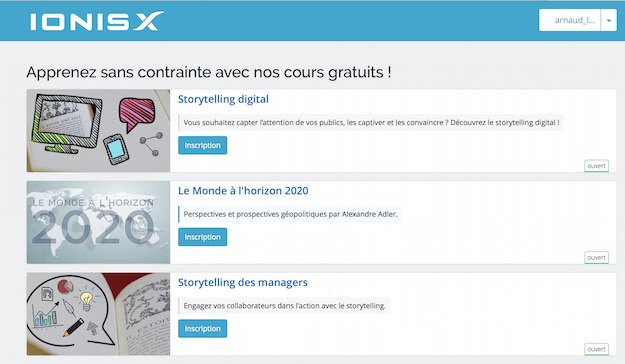
Communication
Clear communication is vital for the successful management of projects. Project failures often stem from miscommunication. Communication should have a clear goal. It should also be clear about what it is meant to achieve. Communication should consider the differences between intended recipients and their experiences. Communication is an important principle for project management, no matter what your role. Here are some tips to help improve communication.
FAQ
What is the difference between Six Sigma Six Sigma and TQM?
The main difference between these two quality management tools is that six sigma focuses on eliminating defects while total quality management (TQM) focuses on improving processes and reducing costs.
Six Sigma can be described as a strategy for continuous improvement. This method emphasizes eliminating defects using statistical methods such p-charts, control charts, and Pareto analysis.
This method seeks to decrease variation in product output. This is done by identifying and correcting the root causes of problems.
Total quality management involves measuring and monitoring all aspects of the organization. Training employees is also part of total quality management.
It is often used to increase productivity.
What are management concepts?
Management Concepts are the management principles and practices that managers use in managing people and resources. They cover topics like job descriptions (job descriptions), performance evaluations, training programmes, employee motivation and compensation systems.
What is the difference of leadership and management?
Leadership is about inspiring others. Management is about controlling others.
Leaders inspire others, managers direct them.
A leader motivates people to achieve success; a manager keeps workers on task.
A leader develops people; a manager manages people.
What is Six Sigma?
It's a method for quality improvement that focuses on customer service as well as continuous learning. The objective is to eliminate all defects through statistical methods.
Motorola invented Six Sigma in 1986 as part its efforts to improve manufacturing.
The idea spread quickly in the industry. Today many organizations use six-sigma techniques to improve product design.
Statistics
- The profession is expected to grow 7% by 2028, a bit faster than the national average. (wgu.edu)
- The BLS says that financial services jobs like banking are expected to grow 4% by 2030, about as fast as the national average. (wgu.edu)
- Hire the top business lawyers and save up to 60% on legal fees (upcounsel.com)
- The average salary for financial advisors in 2021 is around $60,000 per year, with the top 10% of the profession making more than $111,000 per year. (wgu.edu)
- Your choice in Step 5 may very likely be the same or similar to the alternative you placed at the top of your list at the end of Step 4. (umassd.edu)
External Links
How To
What is Lean Manufacturing?
Lean Manufacturing uses structured methods to reduce waste, increase efficiency and reduce waste. They were developed by Toyota Motor Corporation in Japan during the 1980s. The aim was to produce better quality products at lower costs. Lean manufacturing is about eliminating redundant steps and activities from the manufacturing process. It has five components: continuous improvement and pull systems; just-in time; continuous change; and kaizen (continuous innovation). Pull systems are able to produce exactly what the customer requires without extra work. Continuous improvement is constantly improving upon existing processes. Just-in time refers to components and materials being delivered right at the place they are needed. Kaizen refers to continuous improvement. It is achieved through small changes that are made continuously. The 5S acronym stands for sort in order, shine standardize and maintain. To achieve the best results, these five elements must be used together.
Lean Production System
Six key concepts underlie the lean production system.
-
Flow - focuses on moving information and materials as close to customers as possible.
-
Value stream mapping- This allows you to break down each step of a process and create a flowchart detailing the entire process.
-
Five S's, Sort, Set in Order, Shine. Standardize. and Sustain.
-
Kanban: Use visual signals such stickers, colored tape, or any other visual cues, to keep track your inventory.
-
Theory of constraints: Identify bottlenecks and use lean tools such as kanban boards to eliminate them.
-
Just-in-time delivery - Deliver components and materials right to your point of use.
-
Continuous improvement - make incremental improvements to the process rather than overhauling it all at once.