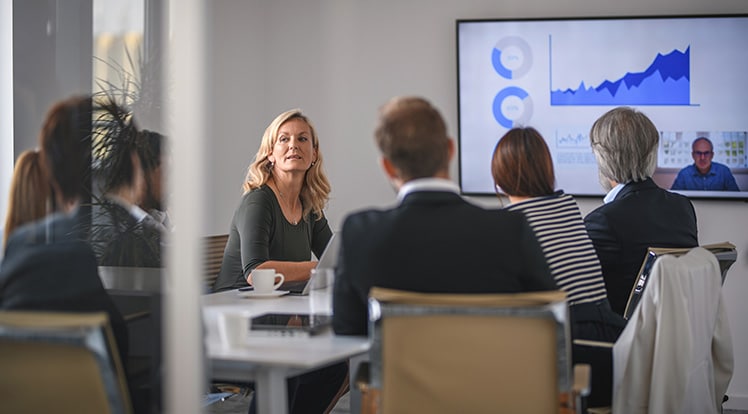
There are many styles of management. Top-down management is just one type. Top-down management emphasizes hierarchy, punishments for employees who don't follow orders, and punishments. This type of management relies on fear and intimidation to keep employees in line. Other types of management emphasize the importance of empathy. Both types of management are equally effective. Contact me if there are any questions concerning management. I'd love to answer your questions, and help you find a great job.
Principles of management
The fundamental principle of management is to create a cause-and–effect relationship between actions and their outcomes. In other words, a good management strategy will help you create a link among your actions and the outcomes that you desire. The management principles are universal and can be applied to any organization, no matter its size. This article will cover some of the most important principles and how they can be applied to different types of organizations. For more information, continue reading.
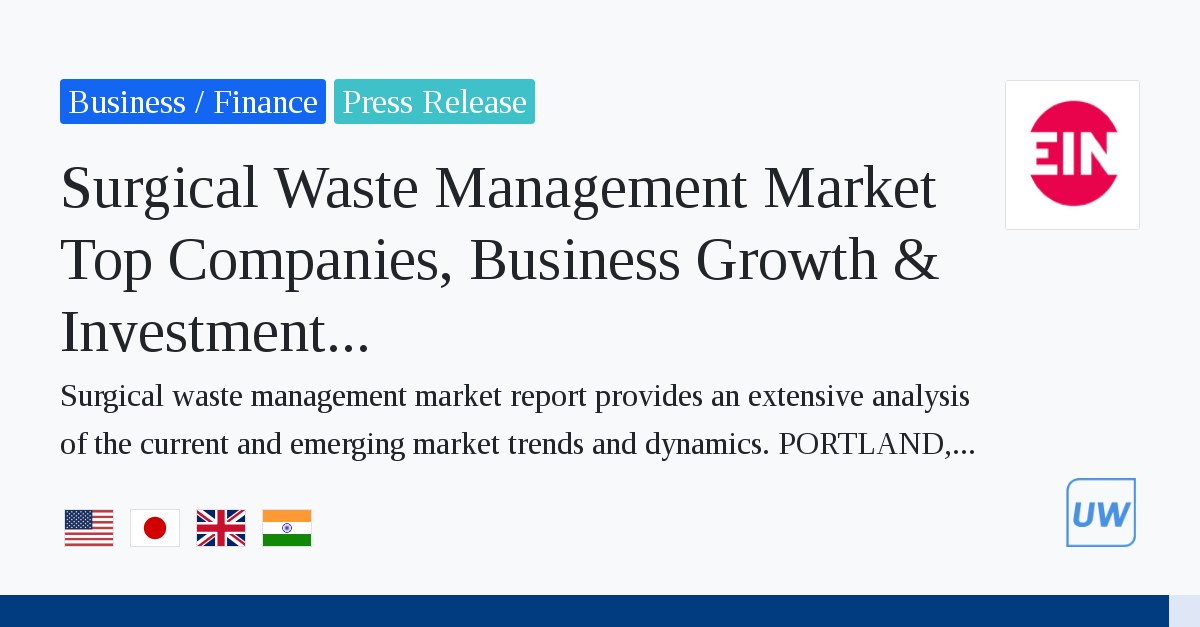
Management functions
Management's main functions are planning, organizing people, staffing and leading. Managers may allocate different amounts of time depending on the organization's level. Planning and organizing are different from leading and controlling which are ongoing processes. The organizing function includes defining a plan and allocating resources in the most efficient manner. The ultimate goal of management is to get to the destination without any difficulties.
Technology's impact on management
Technology has had an enormous impact on business and management. Henri Fayol, a French mine engineer, developed a scientific method of managing a company in the early 1900s. Fayol listed six core functions that managers need to perform. These functions have impacted nearly every department in the majority of companies. Computer hardware and software have revolutionized how work is organised and directed. Managers remained relatively the same but new technologies and processes have dramatically changed how they conduct business.
Management is more effective when empathy is valued
Empathy is not about having feelings or connecting with people. It has many real-world advantages for organizations. Empathy is associated with social and organizational success. However, some of the definitions of empathy have become less accurate as people are becoming increasingly aloof and careless about other people's lives. It can be difficult to feel empathy in such a context. This article provides some tips and tricks to help you increase your empathy in the workplace.
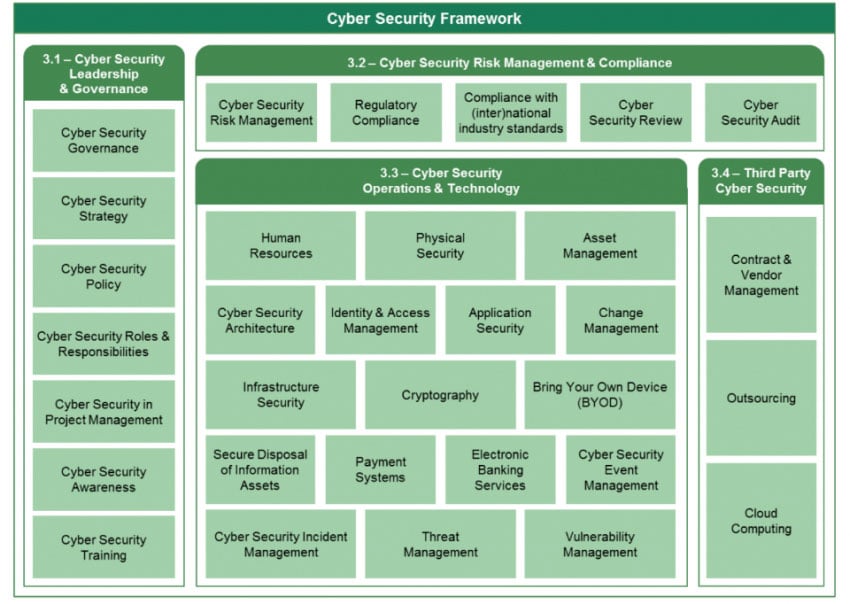
Poor management can lead to high costs
Lost productivity is one of many costs that comes with poor management. Gallup found that one disgruntled individual costs the company $360 million per year. The disengagement of employees is another cost. Both these costs are huge for the business. Poor management is not only a loss in productivity but it also has a negative impact on the bottom-line. Here are five ways poor management can cost businesses money.
FAQ
What role does a manager have in a company's success?
Managers' roles vary from industry to industry.
A manager generally manages the day to-day operations in a company.
He/she ensures the company meets its financial commitments and produces goods/services that customers demand.
He/she ensures that employees follow the rules and regulations and adhere to quality standards.
He/she plans and oversees marketing campaigns.
How do you define Six Sigma?
Six sigma is a common concept for people who have worked in statistics or operations research. Anyone involved in business can benefit.
Because it requires a high degree of commitment, only leaders with strong leadership skills can implement it successfully.
How to manage employees effectively?
Effectively managing employees means making sure they are productive and happy.
This also involves setting clear expectations and monitoring their performance.
Managers must set clear goals for their employees and themselves to achieve this goal.
They need to communicate clearly with staff members. They need to communicate clearly with their staff.
They must also keep track of the activities of their team. These include:
-
What was achieved?
-
How much work was put in?
-
Who did it and why?
-
How did it get done?
-
Why it was done?
This information is useful for monitoring performance and evaluating the results.
What is TQM and how can it help you?
The industrial revolution saw the realization that prices alone were not sufficient to sustain manufacturing companies. This led to the birth of quality. They needed to improve quality and efficiency if they were going to remain competitive.
To address this need for improvement management created Total Quality Management (TQM) which aimed to improve all aspects of an organization's performance. It involved continuous improvement, employee participation, and customer satisfaction.
What are the three basic management styles?
The three major management styles are authoritarian (left-faire), participative and laissez -faire. Each style has strengths and flaws. What style do you prefer? Why?
Authoritarian - The leader sets the direction and expects everyone to comply with it. This style is most effective when an organization is large, stable, and well-run.
Laissez-faire - The leader allows each individual to decide for him/herself. This style is best when the organization has a small but dynamic group.
Participative – Leaders are open to suggestions and ideas from everyone. This style works best in smaller organizations where everyone feels valued.
What is the difference between Six Sigma Six Sigma and TQM?
The main difference between these two quality-management tools is that six-sigma concentrates on eliminating defects while total QM (TQM), focuses upon improving processes and reducing expenses.
Six Sigma can be described as a strategy for continuous improvement. It emphasizes the elimination and improvement of defects using statistical methods, such as control charts, P-charts and Pareto analysis.
This method aims to reduce variation in product production. This is achieved by identifying and addressing the root causes of problems.
Total quality management involves measuring and monitoring all aspects of the organization. This includes training employees to improve their performance.
It is frequently used as an approach to increasing productivity.
Statistics
- 100% of the courses are offered online, and no campus visits are required — a big time-saver for you. (online.uc.edu)
- Hire the top business lawyers and save up to 60% on legal fees (upcounsel.com)
- Our program is 100% engineered for your success. (online.uc.edu)
- UpCounsel accepts only the top 5 percent of lawyers on its site. (upcounsel.com)
- As of 2020, personal bankers or tellers make an average of $32,620 per year, according to the BLS. (wgu.edu)
External Links
How To
How is Lean Manufacturing done?
Lean Manufacturing processes are used to reduce waste and improve efficiency through structured methods. These processes were created by Toyota Motor Corporation, Japan in the 1980s. The goal was to produce quality products at lower cost. Lean manufacturing seeks to eliminate unnecessary steps and activities in the production process. It has five components: continuous improvement and pull systems; just-in time; continuous change; and kaizen (continuous innovation). Pull systems involve producing only what the customer wants without any extra work. Continuous improvement is constantly improving upon existing processes. Just-in-time refers to when components and materials are delivered directly to the point where they are needed. Kaizen is continuous improvement. This can be achieved by making small, incremental changes every day. Fifth, the 5S stand for sort, set up in order to shine, standardize, maintain, and standardize. To achieve the best results, these five elements must be used together.
Lean Production System
The lean production system is based on six key concepts:
-
Flow - focus on moving material and information as close to customers as possible;
-
Value stream mapping is the ability to divide a process into smaller tasks, and then create a flowchart that shows the entire process.
-
Five S's, Sort, Set in Order, Shine. Standardize. and Sustain.
-
Kanban is a visual system that uses visual cues like stickers, colored tape or stickers to keep track and monitor inventory.
-
Theory of constraints: identify bottlenecks in your process and eliminate them using lean tools, such as kanban board.
-
Just-in-time - deliver components and materials directly to the point of use;
-
Continuous improvement - make incremental improvements to the process rather than overhauling it all at once.