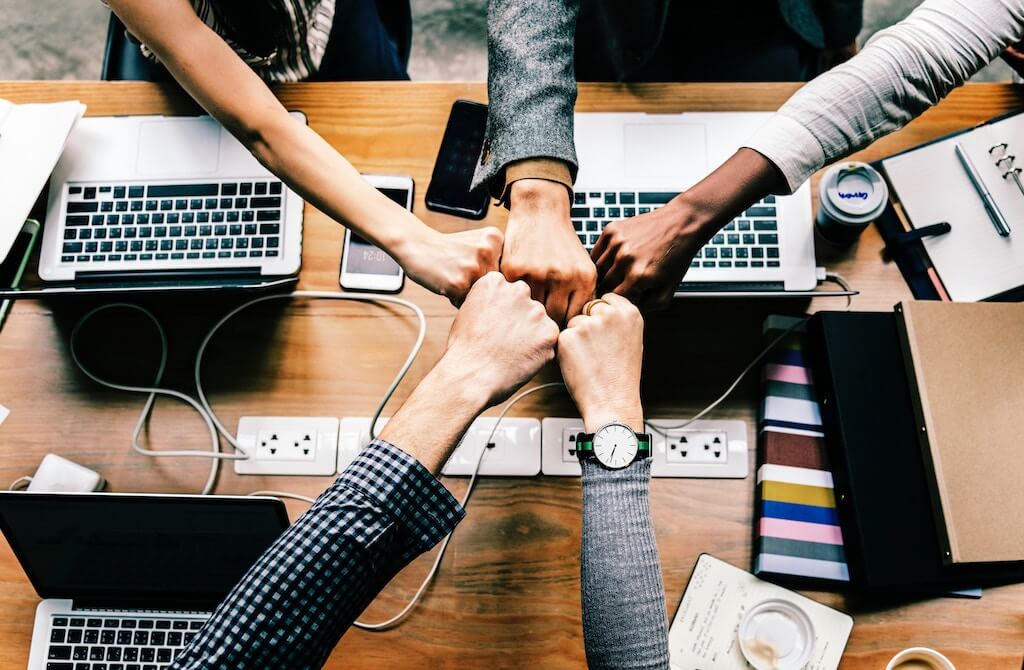
You will need a degree in supply management to be able to pursue a career. A degree in supply chain management will help you take the leadership role in a business organization. This involves operational, tactical, and strategic levels. It also helps improve organizational performance. It requires excellent communication skills.
Supply chain management can also include project management.
Supply chain management, which is essential for any business, is important. Project management can help improve the management of your supply chain. Project management is a process that allows you to create and implement an organization plan. The main goal of a project is to produce a completed project that meets the specified goals and success criteria. A project manager ensures that the products and services you order are delivered on time. Project management can bring many advantages such as increased collaboration, cost-savings, quality controls, and risk mitigation. There are also some drawbacks to project management.
Although strategy and tactics are essential, they can't be implemented without planning. Without clear direction, a strategy can go wrong and cause a project to fail. The process of project management is crucial to successful implementation of a supply chain project. Project managers can use best practices to implement solutions and create new strategies to meet current needs.
It covers tactical, strategic and operational levels.
A supply chain can be divided into three main levels: tactical, strategic, and operational. Supply chain success is dependent on the strategic level. It sets the foundation for all levels. It involves collecting and analysing data, evaluating the major factors that affect the supply chain, and making decisions based on that information. Although operational decisions are taken to satisfy customer requirements, strategic decisions are vital to the overall success and sustainability of the supply chain.
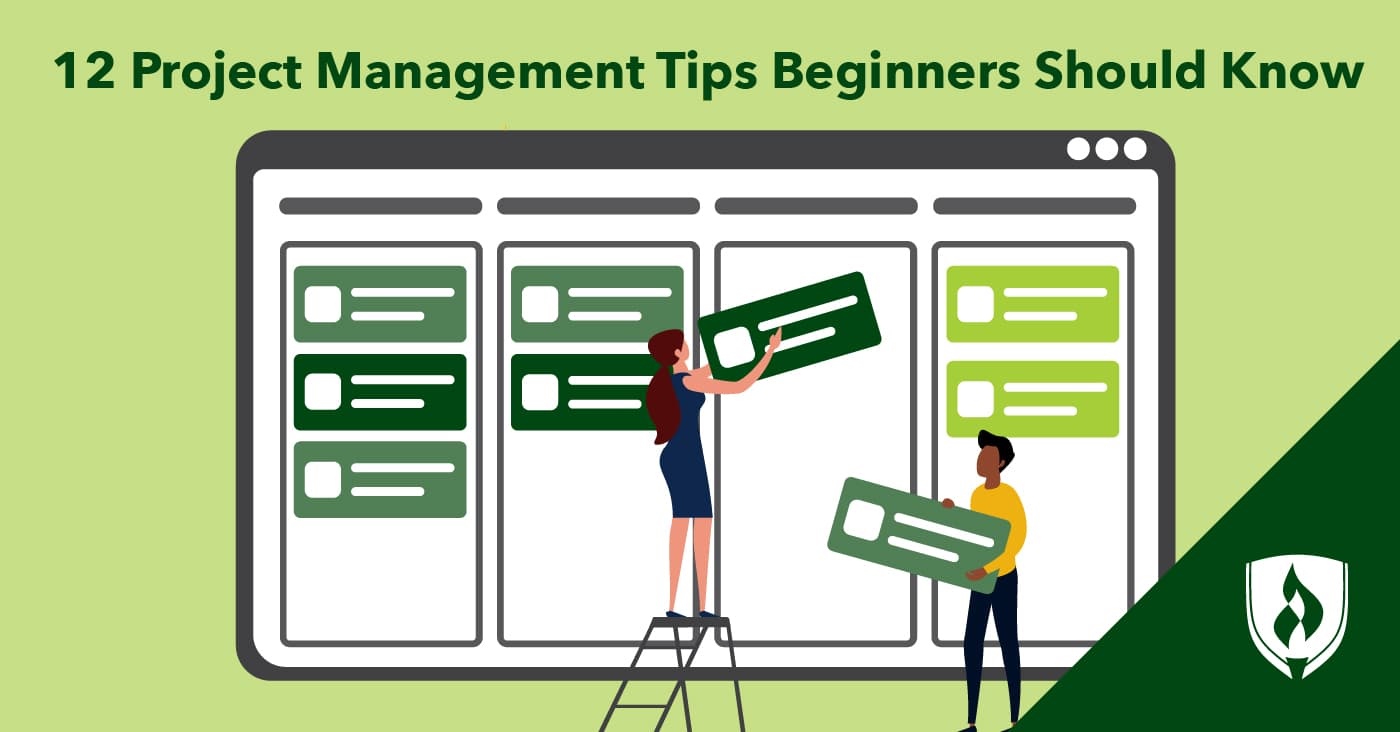
The strategic level outlines the overall company objectives and identifies strengths and weaknesses and develops a vision for the future. The tactical level is about executing plans to achieve the strategy and taking steps to accomplish them. These plans may include inventory management, forecasting, production scheduling and shipping. Some analysts believe that the strategic level is now more important due to the globalization.
It improves organization performance
It is the ability of a supply chain manager to improve organizational performance that determines its effectiveness. You can measure and assess supply chain performance using a number of methods including customer relationship management (CRM), inner supply chain management and information sharing. These methods all help to improve organizational performance.
Supply chains are not all created equal. Some organizations have never designed a cohesive supply chain structure. This can result in different functions reporting to different parents functions, or even at different points within a single parent function. This can lead confusion and slow response time to critical issues. As an example: Demand planning processes might report to the supply-chain manager in one country, but not to the sales managers in another. These organizational problems can result in significant inefficiencies.
It requires communication skills
A strong set of communication skills is necessary to succeed in supply chain management. Supply chain leaders must communicate complex ideas clearly and encourage collaboration. Additionally, they should be able to produce accurate reports. These skills will increase your career opportunities. Consider furthering your education to get certified in supply chain management.
You will be interacting with many people as a supply chain manager. This requires you to have a high level of empathy and the ability to listen actively. Your leadership skills may be reduced if you lack empathy, especially in times of change. You may make employees feel unappreciated or rejected if they don't understand your concerns. This is why it is so important to learn about yourself and enhance your skills.
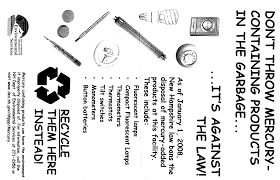
It can lead you to a career with supply chain management
Many career opportunities are available with a degree in supply chain management. Supply chain managers manage a wide variety of processes from the initial forecasting of consumer demand to the finished product on store shelves. This job requires the management of a complex network of vendors and people. To be successful, supply chain managers need to be proficient in both business management and computer science.
You can either complete your degree in supply-chain management online or in the traditional classroom setting. Your training will be similar to a 4-year program. Online programs have less networking opportunities but offer the same quality training as traditional schools. You'll also need strong analytical skills and a love of working with data and forecasts. An online degree program will also prepare you to teach the technical aspects of supply chain management to others.
FAQ
What is a simple management tool that aids in decision-making and decision making?
The decision matrix is a powerful tool that managers can use to help them make decisions. It allows them to consider all possible solutions.
A decision matrix allows you to represent alternatives as columns and rows. This allows you to easily see how each choice affects others.
This example shows four options, each represented by the boxes on either side of the matrix. Each box represents a different option. The top row depicts the current status quo, while the bottom row represents what would happen if no action was taken.
The effect of selecting Option 1 is shown in the middle column. In this case, it would mean increasing sales from $2 million to $3 million.
The results of choosing Option 2 and 3 can be seen in the columns below. These are good changes, they increase sales by $1million or $500,000. These positive changes have their downsides. Option 2 can increase costs by $100 million, while Option 3 can reduce profits by $200,000.
The last column displays the results of selecting Option 4. This will result in sales falling by $1,000,000
The best thing about using a decision matrix is that you don't need to remember which numbers go where. The best thing about a decision matrix is that you can simply look at the cells, and immediately know whether one option is better or not.
This is because your matrix has already done the hard work. It's simply a matter of comparing the numbers in the relevant cells.
Here's an example of how you might use a decision matrix in your business.
Decide whether you want to invest more in advertising. This will allow you to increase your revenue by $5000 per month. However, this will mean that you'll have additional expenses of $10,000.
The net result of advertising investment can be calculated by looking at the cell below that reads "Advertising." It is 15 thousand. Advertising is worth much more than the investment cost.
What are management principles?
Management Concepts are the principles and practices managers use to manage people and resources. These include topics such as human resource policies and job descriptions, performance assessments, training programs and employee motivation.
What is Kaizen and how can it help you?
Kaizen, a Japanese term that means "continuous improvement," is a philosophy that encourages employees and other workers to continuously improve their work environment.
Kaizen is built on the belief that everyone should be able do their jobs well.
Why is it important that companies use project management methods?
Project management techniques can be used to ensure smooth project execution and meeting deadlines.
This is because most businesses rely on project work for their products and services.
Companies must manage these projects effectively and efficiently.
Companies that do not manage their projects effectively risk losing time, money, or reputation.
What is Six Sigma, exactly?
This is a method of quality improvement that emphasizes customer service, continuous learning, and customer service. It is a method that eliminates defects using statistical techniques.
Motorola developed Six Sigma in 1986 to help improve its manufacturing processes.
It was quickly adopted by the industry and many companies are now using six-sigma to improve product design, production, delivery, customer service, and product design.
What are the five management steps?
The five stages of any business are planning, execution, monitoring, review, and evaluation.
Planning involves setting goals for the future. Planning involves defining your goals and how to get there.
Execution occurs when you actually carry out the plans. These plans must be adhered to by everyone.
Monitoring is the process of evaluating your progress toward achieving your objectives. Regular reviews of performance against budgets and targets should be part of this process.
At the end of every year, reviews take place. They provide an opportunity to assess whether everything went well during the year. If not, changes may be made to improve the performance next time around.
After each year's review, evaluation occurs. It helps you identify the successes and failures. It also provides feedback on how well people performed.
Statistics
- Our program is 100% engineered for your success. (online.uc.edu)
- 100% of the courses are offered online, and no campus visits are required — a big time-saver for you. (online.uc.edu)
- As of 2020, personal bankers or tellers make an average of $32,620 per year, according to the BLS. (wgu.edu)
- UpCounsel accepts only the top 5 percent of lawyers on its site. (upcounsel.com)
- The average salary for financial advisors in 2021 is around $60,000 per year, with the top 10% of the profession making more than $111,000 per year. (wgu.edu)
External Links
How To
How does Lean Manufacturing work?
Lean Manufacturing techniques are used to reduce waste while increasing efficiency by using structured methods. These processes were created by Toyota Motor Corporation, Japan in the 1980s. The main goal was to produce products at lower costs while maintaining quality. Lean manufacturing is about eliminating redundant steps and activities from the manufacturing process. It is composed of five fundamental elements: continuous improvement; pull systems, continuous improvements, just-in–time, kaizen, continuous change, and 5S. Pull systems are able to produce exactly what the customer requires without extra work. Continuous improvement means continuously improving on existing processes. Just-in time refers to components and materials being delivered right at the place they are needed. Kaizen refers to continuous improvement. It is achieved through small changes that are made continuously. The 5S acronym stands for sort in order, shine standardize and maintain. These five elements work together to produce the best results.
Lean Production System
Six key concepts are the basis of lean production:
-
Flow - focuses on moving information and materials as close to customers as possible.
-
Value stream mapping is the ability to divide a process into smaller tasks, and then create a flowchart that shows the entire process.
-
Five S’s - Sorted, In Order. Shine. Standardize. And Sustain.
-
Kanban: Use visual signals such stickers, colored tape, or any other visual cues, to keep track your inventory.
-
Theory of constraints: identify bottlenecks in your process and eliminate them using lean tools, such as kanban board.
-
Just-in Time - Send components and material directly to the point-of-use;
-
Continuous improvement: Make incremental improvements to the process instead of overhauling it completely.