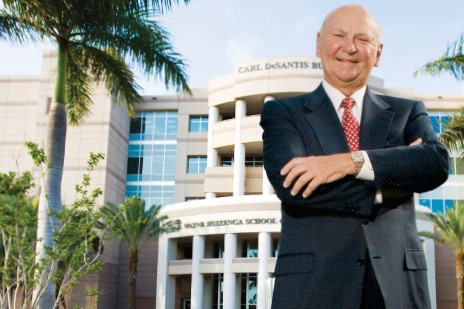
Risk Management is the management of risk to reduce the likelihood of an organization suffering loss or damage. This includes planning for possible negative outcomes as well as reducing the chances of profit-chasing and escalated situations. This is essential for any company's success. Risk management has many benefits. Here are some examples.
Reduces the possibility of adverse reactions
To be effective in managing risk, you must first establish an objective and a system of evaluating and reducing the risks. Risk management is difficult because it runs counter to many of the biases that we have as humans. Rules and compliance can help to mitigate some risks, but not all. Risk management must be active, which means that managers need to think about risks systematically, institute processes that address these risks, and monitor and manage the risks accordingly.
Reduces the probability of escalation
By establishing game plans for a range of situations that can lead to an escalation, risk management can significantly reduce the chance of escalation. Even though most risks do not have a predetermined end point to them, having a plan will help you be ready for whatever happens. This will help reduce the chances of escalation and minimize damage.
Reduces profit-chasing
It is becoming a popular topic to talk about risk management. Risk management is the act of taking steps to minimize potential losses. For example, airlines can use financial derivatives in order to protect themselves from an increase fuel prices. In order to protect their buildings from earthquakes, companies can raise their construction costs. In order to reduce their costs, companies may work with others that are facing similar risks.
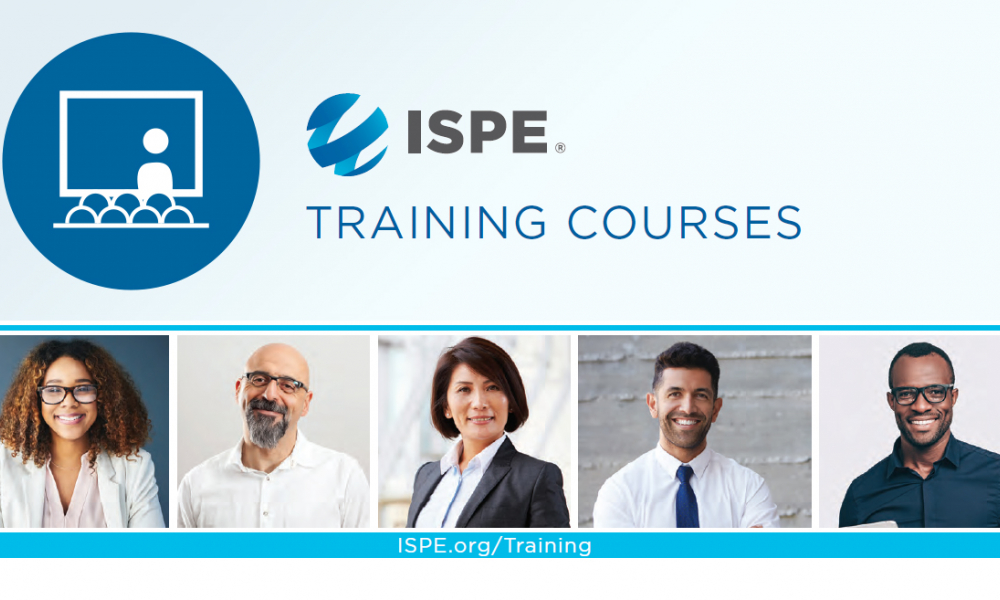
FAQ
What is the difference of a program and project?
A project is temporary, while a program lasts forever.
A project usually has a specific goal and deadline.
It is often carried out by a team of people who report back to someone else.
A program will usually have a set number of goals and objectives.
It is often done by one person.
What are the steps that management takes to reach a decision?
Managers have to make complex decisions. It involves many factors, such as analysis and strategy, planning, execution, measurement, evaluation, feedback etc.
When managing people, the most important thing to remember is that they are just human beings like you and make mistakes. You are always capable of improving yourself, and there's always room for improvement.
This video explains the process of decision-making in Management. We will discuss the various types of decisions, and why they are so important. Every manager should be able to make them. The following topics will be covered.
What is the main difference between Six Sigma Six Sigma TQM and Six Sigma Six Sigma?
The main difference in these two quality management tools lies in the fact that six sigma is focused on eliminating defects and total quality management (TQM), emphasizes improving processes and reducing costs.
Six Sigma is a methodology for continuous improvement. It emphasizes the elimination or minimization of defects through statistical methods such control charts and p charts.
This method seeks to decrease variation in product output. This is done by identifying root causes and rectifying them.
Total quality management is the measurement and monitoring of all aspects within an organization. It also includes training employees to improve performance.
It is often used to increase productivity.
What is a basic management tool that can be used for decision-making?
A decision matrix is an easy but powerful tool to aid managers in making informed decisions. It helps them to think strategically about all options.
A decision matrix can be used to show alternative options as rows or columns. This allows one to see how each alternative impacts other options.
In this example, we have four possible alternatives represented by the boxes on the left side of the matrix. Each box represents an option. The top row displays the current situation, and the bottom row shows what might happen if nothing is done.
The effect of choosing Option 1 can be seen in column middle. In this case, it would mean increasing sales from $2 million to $3 million.
The effects of options 2 and 3 are shown in the next columns. These positive changes result in increased sales of $1 million and $500,000. But, they also have some negative consequences. For instance, Option 2 increases cost by $100 thousand while Option 3 reduces profits by $200 thousand.
The final column shows results of choosing Option 4. This results in a decrease of sales by $1,000,000
The best part about using a decision matrix to guide you is that you don’t need to keep track of which numbers go where. The best thing about a decision matrix is that you can simply look at the cells, and immediately know whether one option is better or not.
The matrix has already done all of the work. It's simply a matter of comparing the numbers in the relevant cells.
Here's a sample of how you might use decision matrixes in your business.
You need to decide whether to invest in advertising. This will allow you to increase your revenue by $5000 per month. However, additional expenses of $10 000 per month will be incurred.
If you look at the cell that says "Advertising", you can see the number $15,000. Advertising is worth much more than the investment cost.
What is Six Sigma and how can it help you?
It's an approach to quality improvement that emphasizes customer service and continuous learning. It is a method that eliminates defects using statistical techniques.
Motorola invented Six Sigma in 1986 as part its efforts to improve manufacturing.
The idea spread quickly in the industry. Today many organizations use six-sigma techniques to improve product design.
Statistics
- Your choice in Step 5 may very likely be the same or similar to the alternative you placed at the top of your list at the end of Step 4. (umassd.edu)
- 100% of the courses are offered online, and no campus visits are required — a big time-saver for you. (online.uc.edu)
- The profession is expected to grow 7% by 2028, a bit faster than the national average. (wgu.edu)
- As of 2020, personal bankers or tellers make an average of $32,620 per year, according to the BLS. (wgu.edu)
- This field is expected to grow about 7% by 2028, a bit faster than the national average for job growth. (wgu.edu)
External Links
How To
How do I do the Kaizen Method?
Kaizen means continuous improvement. The Japanese philosophy emphasizes small, incremental improvements to achieve continuous improvement. This term was created by Toyota Motor Corporation in 1950. It's a team effort to continuously improve processes.
Kaizen, a Lean Manufacturing method, is one of its most powerful. Employees responsible for the production line should identify potential problems in the manufacturing process and work together to resolve them. This is how you can improve the quality and lower the cost.
Kaizen is a way to raise awareness about what's happening around you. So that there is no problem, you should immediately correct it if something goes wrong. Report any problem you see at work to your manager.
Kaizen is based on a few principles. When working with kaizen, we always start with the end result and move towards the beginning. To improve our factory, for example, we need to fix the machines that produce the final product. First, we fix machines that produce components. Next, we fix machines that produce raw material. And finally, we fix the workers who work directly with those machines.
This approach is called 'kaizen' because it focuses on improving everything steps by step. After we're done with the factory, it's time to go back and fix the problem.
Before you can implement kaizen into your business, it is necessary to learn how to measure its effectiveness. There are many ways to tell if kaizen is effective. One method is to inspect the finished products for defects. Another way to find out how productive your company has been since you implemented kaizen is to measure the increase in productivity.
To determine if kaizen is effective, you should ask yourself why you chose to implement kaizen. Was it just because it was the law or because you wanted to save money? Did you really believe that it would be a success factor?
Congratulations! You're ready to start kaizen.