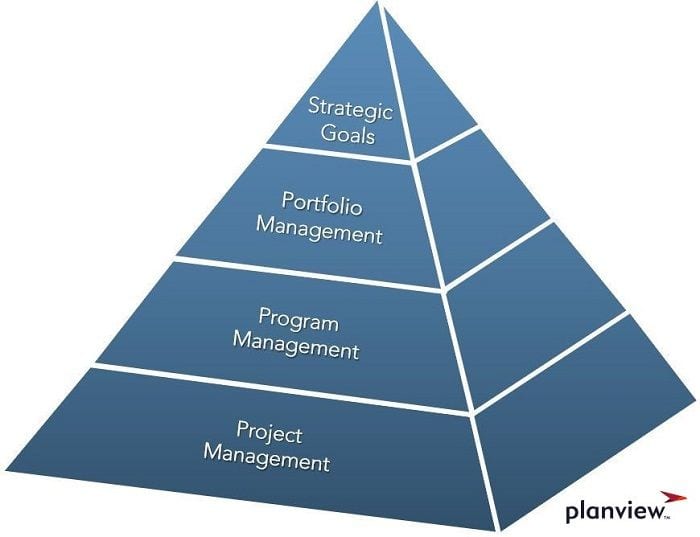
Industrial waste management is the collection, transportation, and disposal of hazardous waste. To avoid contamination of surrounding areas, hazardous waste is usually disposed in a modern secure facility. This can be costly, as it requires the creation of a new location and transportation of large volumes. The other option is on-site remediation, which involves the construction of a new facility at the original location and treatment of water pollution contamination. Some plants use complete containment. This means the site is sealed off and groundwater flow reduced.
Construction and demolition scrap
Construction and demolition debris is an industrial waste generated during construction. Most construction waste can be legally disposed of in landfills. In some places, however, illegally dumped waste on land and in water bodies is possible. It can also be dangerous for the environment and violates regulations that protect commerce and human health. In the United States alone, millions of tons of building-related waste are dumped in landfills each year. As such, it is essential for construction waste management to adhere to strict regulations.
Fabrication of waste
A circular economy is all about managing manufacturing waste. As energy and resources are being conserved, so has the use of recycled material. There are many technologies available today to assist manufacturers in managing and recycling their waste. Some technologies can help manufacturers reduce their costs while increasing their output.

Agriculture waste
Agriculture waste can be defined as solid waste generated by agricultural processes. This includes wastes generated during animal and crop production, food and meat processing, and waste from animal feeding. These solid wastes include animal carcasses and waste from animal feeding, feathers and hoofs, as well as crop residues.
Chemical waste
A majority of chemical wastes are hazardous. This means that they pose a danger to the environment and human health. There are regulations that cover how hazardous wastes should be disposed of. Incorrect disposal of hazardous materials can also lead to heavy environmental penalties. However, certain types of wastes are not considered hazardous so they are not subject the same regulations.
Mining waste
Mining generates a lot of waste. Therefore, it is vital that miners learn how to dispose of and manage this waste. Erich Lawson, a freelance writer, is passionate about environmental issues. Erich Lawson writes on a wide range of recycling topics including balers and compactors, as well how to manage industrial waste. He loves helping businesses reduce their garbage costs and increase their revenue through recycling.
Oil & natural gas waste
Oil and gas wastes are subject to specific management requirements. Oil & Gas wastes can be classified into three categories: production fluids, drilling wastes, and made waters. These materials should be disposed carefully to reduce their impact on our environment.
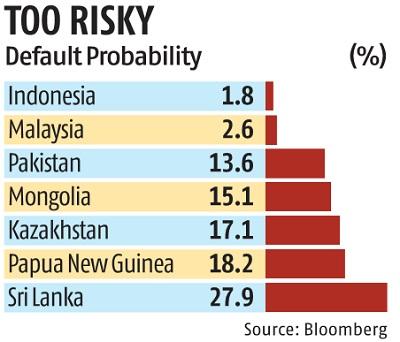
Nuclear waste
Solid waste must be properly disposed of to protect public health and improve the environment. Specially constructed engineering modules can safely dispose of waste with a shorter half-life (less that 100 years), such as reinforced concrete trenches and tile holes or stone lined trenches. Near Surface Disposal Facility (NSDF), which is located below the earth, is where waste is buried to a depth of up to 500 m. Multi-barrier systems are used to stop radioactive waste from spreading.
Others
Global industrial waste management is fragmented. There are many players both local and global. It is important that the industry's major players focus on product innovation when it comes to waste management. The industrial waste management market includes all types of solid, liquid, or gaseous waste from various industrial sectors. Wastes from these sectors may include hazardous and non-hazardous materials. Many of these materials can be disposed of in a landfill or incinerated. These practices can cause severe damage to the wildlife and environment.
FAQ
What are the four main functions of management?
Management is responsible in planning, organizing and directing people and resources. It includes the development of policies and procedures as well as setting goals.
Management assists an organization in achieving its goals by providing direction, coordination and control, leadership, motivation, supervision and training, as well as evaluation.
The following are the four core functions of management
Planning - Planning refers to deciding what is needed.
Organizing: Organizing refers to deciding how things should work.
Directing - Directing means getting people to follow instructions.
Controlling – This refers to ensuring that tasks are carried out according to plan.
What role can a manager fill in a company’s management?
The role of a manager varies from one industry to another.
A manager generally manages the day to-day operations in a company.
He/she is responsible for ensuring that the company meets all its financial obligations and produces the goods or services customers want.
He/she is responsible for ensuring that employees comply with all regulations and follow quality standards.
He/she plans and oversees marketing campaigns.
What is the main difference between Six Sigma Six Sigma TQM and Six Sigma Six Sigma?
The key difference between the two quality management tools is that while six-sigma focuses its efforts on eliminating defects, total quality management (TQM), focuses more on improving processes and reducing cost.
Six Sigma is a methodology for continuous improvement. It emphasizes the elimination and improvement of defects using statistical methods, such as control charts, P-charts and Pareto analysis.
This method seeks to decrease variation in product output. This is done by identifying and correcting the root causes of problems.
Total quality management includes monitoring and measuring all aspects of an organization's performance. Training employees is also part of total quality management.
It is used to increase productivity.
Why is it so important for companies that they use project management techniques
Project management techniques are used to ensure that projects run smoothly and meet deadlines.
This is because many businesses depend heavily upon project work to produce products and services.
These projects are essential for companies.
Companies may lose their reputation, time and money if they do not have effective project management.
What are the five management process?
The five stages of a business include planning, execution (monitoring), review, evaluation, and review.
Planning involves setting goals for the future. This includes setting goals for the future and defining what you want.
Execution happens when you actually do the plan. They must be followed by all parties.
Monitoring is the act of monitoring your progress towards achieving your targets. Monitoring should include regular reviews of performance against goals and budgets.
Reviews take place at the end of each year. They allow for an assessment of whether all went well throughout the year. If not, changes may be made to improve the performance next time around.
After the annual review, evaluation takes place. It helps to identify what went well and what didn’t. It also provides feedback on the performance of people.
What are the three main management styles you can use?
These are the three most common management styles: participative (authoritarian), laissez-faire (leavez-faire), and authoritarian. Each style has strengths and flaws. Which style do yo prefer? Why?
Autoritarian – The leader sets the direction for everyone and expects them to follow. This style works best in large organizations that are stable and well-organized.
Laissez-faire – The leader gives each individual the freedom to make decisions for themselves. This style works best when the organization is small and dynamic.
Participative - Leaders listen to all ideas and suggestions. This style works best in smaller organizations where everyone feels valued.
Statistics
- Hire the top business lawyers and save up to 60% on legal fees (upcounsel.com)
- As of 2020, personal bankers or tellers make an average of $32,620 per year, according to the BLS. (wgu.edu)
- Your choice in Step 5 may very likely be the same or similar to the alternative you placed at the top of your list at the end of Step 4. (umassd.edu)
- UpCounsel accepts only the top 5 percent of lawyers on its site. (upcounsel.com)
- 100% of the courses are offered online, and no campus visits are required — a big time-saver for you. (online.uc.edu)
External Links
How To
How can you create a Quality Management Plan, (QMP)?
The Quality Management Plan (QMP) was established in ISO 9001. It is a systematic way to improve processes, products and services. It emphasizes on how to continuously measure, analyze, control, and improve processes, product/service, and customer satisfaction.
QMP is a standard way to improve business performance. QMP's goal is to improve service delivery and production. QMPs should address all three dimensions: Products, Services, and processes. When the QMP includes only one aspect, it is called a "Process" QMP. The QMP that focuses on a Product/Service is called a "Product." QMP. QMP is also used to refer to QMPs that focus on customer relations.
When implementing a QMP, there are two main elements: Scope and Strategy. They can be described as follows:
Scope: This is the scope of the QMP and its duration. This will be used to define activities that are performed in the first six months of a QMP.
Strategy: This describes the steps taken towards achieving the goals set forth in the scope.
A typical QMP is composed of five phases: Planning Design, Development, Implementation and Maintenance. Each phase is described below:
Planning: In this stage the QMP's objectives and priorities are established. Every stakeholder involved in the project is consulted to determine their expectations and needs. Once the objectives and priorities have been identified, it is time to plan the strategy to achieve them.
Design: The design stage involves the development of vision, mission strategies, tactics, and strategies that will allow for successful implementation. These strategies can be implemented through the creation of detailed plans.
Development: Here, the development team works towards building the necessary capabilities and resources to support the implementation of the QMP successfully.
Implementation is the actual implementation of QMP according to the plans.
Maintenance: The maintenance of the QMP is an ongoing task.
Additional items must be included in QMP.
Stakeholder involvement is important for the QMP's success. They are required to actively participate in the planning, design and development of the QMP, as well as the implementation and maintenance phases.
Project Initiation. It is important to understand the problem and the solution in order to initiate any project. This means that the initiator should know why they want something done and what they hope for from the end result.
Time frame: The QMP's timeframe is critical. For a short time, you can start with the simple version of the QMP. For a long-term commitment you may need more complicated versions.
Cost Estimation: Cost estimation is another vital component of the QMP. Without knowing how much you will spend, planning is impossible. The QMP should be cost-estimated before it can begin.
QMPs are not just a written document. They should be a living document. It can change as the company grows or changes. It should be reviewed on a regular basis to ensure that it is still meeting the company's needs.