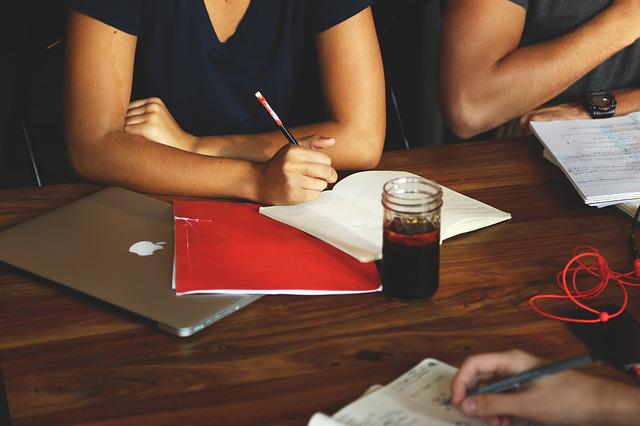
Global supply chains management is a practice that manages the distribution of goods, services and products across an entire transnational company's network. The goal is to maximize profit and minimize waste. Many methods can be used to improve efficiency, such as the creation of software tools to track the entire process. This article looks at some of the key benefits and requirements of a global supply chain management degree program. This article also addresses the education requirements for students interested in this field.
Benefits of a global supply-chain management degree
A degree in Global Supply Chain Management is an excellent option if you're interested in a career that involves global supply-chain management. This degree program will prepare your for a career as a global leader. Graduates will have advanced knowledge of supply chain management and advanced analytical skills. They will also learn how to optimize commercial networks. If you are already working, a degree in global supply chain management can help you advance your career.
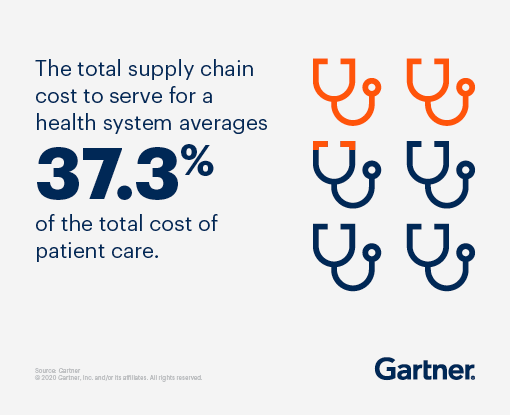
The curriculum will focus on the details of operations including production planning, inventory control, warehousing and global supplier relationships. Students will be taught how to maintain and develop healthy relationships with suppliers all over the globe. The program includes both applied coursework and research. This allows students to gain real-world experience and learn the ropes of this industry. After graduation, you will also be eligible to work in your chosen industry.
There are numerous career opportunities available to graduates of the program.
Global supply chain management offers many job opportunities across a range of industries. Many companies need to manage their expenses, including labor hours as well as materials. Global supply chain management is a career that could allow you to help companies make more money. Depending on what type of job you choose, your role could include managing all aspects of the supply chain. Although the career opportunities available to a global supply chain management graduate are varied, these are some of the most popular.
Knowing the supply chain is a key skill that will help you succeed in this job. Candidates should have a thorough understanding of the technicalities of supply chains and be adept at communicating with non-technical colleagues. A background in the Internet Age will give graduates a unique understanding of retail's effects and enable them to help grow e-retail.
Education requirements
A bachelor's degree in business administration is not necessary to become a global supply chain manager. However, a master's degree in global supply chain management will give you the skills and knowledge needed to lead a global supply chain. This degree focuses on the use of advanced analytical tools and technologies to improve the effectiveness commercial networks. This degree can be completed online. This program will help you to develop and implement strategies that can be used for the benefit of your business.
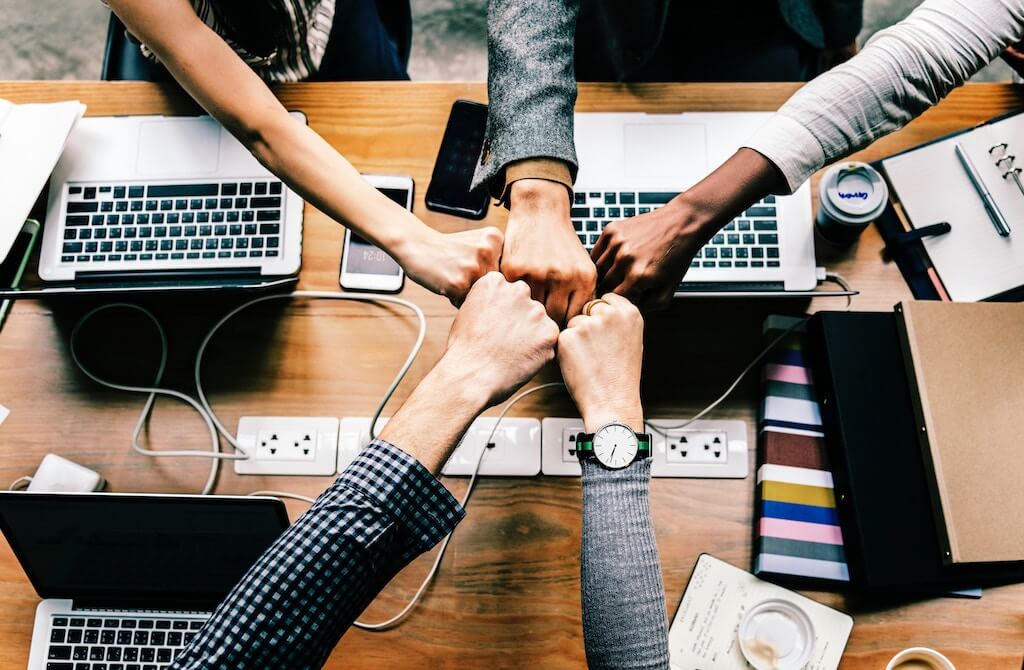
Students who are interested in pursuing a specialization in global supply chain management can also enroll in courses that relate to this field. For example, project management students learn to identify resources, develop budgets, incorporate stakeholder input, and ensure that a project is on track. This program helps students to learn how to interact with global partners as well as the economics of global markets. Students may take courses in leadership or communication skills depending on the program. In addition, they can take business communication courses, which develop their communication skills.
FAQ
Why is it so hard to make smart business decisions?
Complex business systems have many moving parts. People who manage them have to balance multiple priorities while dealing with complexity and uncertainty.
The key to making good decisions is to understand how these factors affect the system as a whole.
This requires you to think about the purpose and function of each component. You then need to consider how those individual pieces interact with each other.
Also, you should ask yourself if there have been any assumptions in your past behavior. If you don't have any, it may be time to revisit them.
You can always ask someone for help if you still have questions after all of this. You may be able to see things from a different perspective than you are and gain insight that can help you find a solution.
What is Six Sigma?
It's a method for quality improvement that focuses on customer service as well as continuous learning. The goal is to eradicate defects through statistical techniques.
Six Sigma was developed at Motorola in 1986 as part of its efforts to improve manufacturing processes.
This idea quickly spread throughout the industry. Today, many organizations use six sigma methods for product design, production and delivery.
How can we create a culture of success in our company?
A successful company culture is one that makes people feel valued and respected.
It's founded on three principal principles:
-
Everyone has something valuable to contribute
-
Fair treatment of people is the goal
-
It is possible to have mutual respect between groups and individuals
These values are reflected in the way people behave. They will treat others with kindness and consideration.
They will listen to other people's opinions respectfully.
And they will encourage others to share ideas and feelings.
Company culture also encourages open communication, collaboration, and cooperation.
People can freely express their opinions without fear or reprisal.
They understand that errors will be tolerated as long they are corrected honestly.
The company culture promotes honesty, integrity, and fairness.
Everyone knows that they must always tell truth.
Everyone is aware that rules and regulations apply to them.
People don't expect special treatment or favors.
What are the five management methods?
Each business has five stages: planning, execution and monitoring.
Planning involves setting goals for the future. It involves setting goals and making plans.
Execution is when you actually execute the plans. Everyone involved must follow them.
Monitoring is the process of evaluating your progress toward achieving your objectives. Regular reviews of performance against budgets and targets should be part of this process.
Every year, there are reviews. They allow for an assessment of whether all went well throughout the year. If not, it is possible to make improvements for next year.
Evaluation takes place after the annual review. It helps to determine what worked and what didn’t. It also gives feedback on how well people did.
What are the main management skills?
Managerial skills are crucial for every business owner, regardless of whether they run a small store in their locality or a large corporation. They are the ability to manage people and finances, space, money, and other factors.
These skills are necessary for setting goals and objectives as well as planning strategies, leading groups, motivating employees and solving problems.
As you can see, there are many managerial responsibilities!
What is TQM?
The industrial revolution was when companies realized that they couldn't compete on price alone. This is what sparked the quality movement. To remain competitive, they had to improve quality as well as efficiency.
Management responded to the need to improve, and developed Total Quality Management (TQM). This focused on improving every aspect of an organization’s performance. It included continuous improvement, employee involvement and customer satisfaction.
How can a manager enhance his/her leadership skills?
You can improve your management skills by practicing them at all times.
Managers must constantly monitor the performance of their subordinates.
It is important to take immediate action if your subordinate doesn't perform as expected.
You should be able to identify what needs improvement and how to improve things.
Statistics
- Our program is 100% engineered for your success. (online.uc.edu)
- Your choice in Step 5 may very likely be the same or similar to the alternative you placed at the top of your list at the end of Step 4. (umassd.edu)
- This field is expected to grow about 7% by 2028, a bit faster than the national average for job growth. (wgu.edu)
- As of 2020, personal bankers or tellers make an average of $32,620 per year, according to the BLS. (wgu.edu)
- The profession is expected to grow 7% by 2028, a bit faster than the national average. (wgu.edu)
External Links
How To
How can Lean Manufacturing be done?
Lean Manufacturing uses structured methods to reduce waste, increase efficiency and reduce waste. They were developed in Japan by Toyota Motor Corporation (in the 1980s). The goal was to produce quality products at lower cost. Lean manufacturing eliminates unnecessary steps and activities from a production process. It has five components: continuous improvement and pull systems; just-in time; continuous change; and kaizen (continuous innovation). Pull systems involve producing only what the customer wants without any extra work. Continuous improvement is constantly improving upon existing processes. Just-intime refers the time components and materials arrive at the exact place where they are needed. Kaizen refers to continuous improvement. It is achieved through small changes that are made continuously. Fifth, the 5S stand for sort, set up in order to shine, standardize, maintain, and standardize. These five elements work together to produce the best results.
Lean Production System
The lean production system is based on six key concepts:
-
Flow is about moving material and information as near as customers can.
-
Value stream mapping- This allows you to break down each step of a process and create a flowchart detailing the entire process.
-
Five S’s - Sorted, In Order. Shine. Standardize. And Sustain.
-
Kanban: Use visual signals such stickers, colored tape, or any other visual cues, to keep track your inventory.
-
Theory of Constraints - Identify bottlenecks in the process, and eliminate them using lean tools such kanban boards.
-
Just-intime - Order components and materials at your location right on the spot.
-
Continuous improvement: Make incremental improvements to the process instead of overhauling it completely.