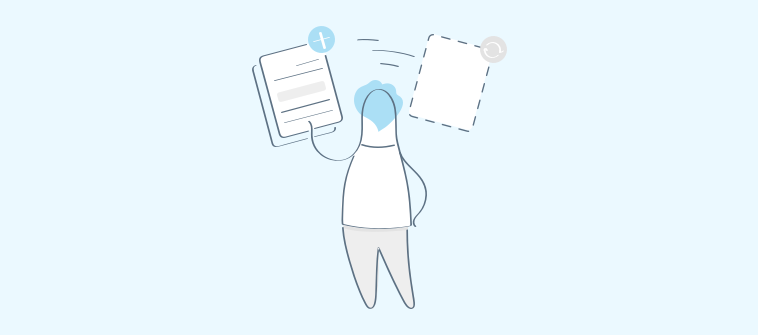
The industrial waste management process involves the collection, transportation and proper disposal. In most cases, hazardous waste is either disposed of in a modern secure facility or removed from the site to avoid contamination of surrounding areas. This process is costly as it involves the preparation of new sites and the transportation of large amounts of waste. Other options include on-site treatment, which involves the construction or renovation of an existing facility and the treatment of any water pollution. Some plants use full containment. This involves the removal of groundwater flow from the area and capping it.
Construction and demolition waste
Construction and demolition refuse is an industrial solid waste. Most construction waste is legally disposed of in landfills. However, in some locations, this waste is illegally dumped on land or in water bodies. Additionally, this waste is illegal and can cause harm to the environment. It also violates laws protecting commerce and human safety. Every year, millions upon millions of tons building-related trash are dumped into landfills in the United States alone. Construction waste management must adhere to strict regulations.
Manufacturing waste
The circular economy includes the management of manufacturing waste. In recent years, the use of recycled materials has increased significantly, as are the amount of energy and materials saved. There are many technologies available today to assist manufacturers in managing and recycling their waste. Manufacturers can reduce costs and increase output with some technologies.
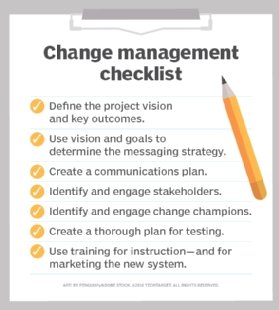
Agriculture waste
Agriculture waste is a result of farming processes. It includes solid and liquid wastes that are generated during animal production, crop growth, and food or meat processing. These solid wastes include animal carcasses and waste from animal feeding, feathers and hoofs, as well as crop residues.
Chemical waste
The majority of chemical waste is hazardous, meaning that it poses a risk to human health or the environment. There are regulations in place that can help you safely dispose of hazardous materials. Incorrect disposal of hazardous materials can also lead to heavy environmental penalties. However, some types of waste are not considered hazardous and, thus, are not subject to the same regulations.
Mining waste
The mining industry produces huge amounts of waste. Mining owners need to know how to properly dispose of this waste. Erich Lawson writes as a freelancer. He is also a passionate environmentalist. Erich Lawson is a freelancer who writes about recycling topics such as compactors or balers as well managing industrial waste. He loves helping businesses reduce their garbage costs and increase their revenue through recycling.
Oil & natural gas waste
For oil and gas wastes, there are specific requirements for industrial waste management. Most common oil & gas hazardous wastes are drilling wastes as well as production fluids and finished waters. These wastes need to be disposed of with care in order to minimize their effect on the environment.
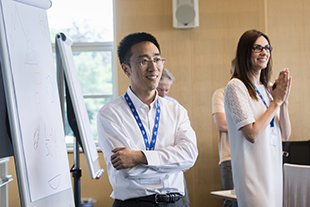
Radioactive waste
The proper disposal of solid waste is vital for public health and the quality of the environment. Specially constructed engineering modules can safely dispose of waste with a shorter half-life (less that 100 years), such as reinforced concrete trenches and tile holes or stone lined trenches. Near Surface Disposal Facility or NSDF is constructed below the ground. Here, the waste can be buried upto 500 metres below ground. Multi-barrier barriers are installed at these facilities to prevent radioactive material from spreading.
Others
Global industrial waste management is fragmented. There are many players both local and global. The industry's key players are focused on innovation in waste management. The market for industrial wastewater management encompasses solid, liquid, as well as gaseous, wastes from different industrial sectors. These wastes may contain hazardous and other non-hazardous substances. Many of these materials can be disposed of in a landfill or incinerated. These practices can cause severe damage to the wildlife and environment.
FAQ
What kind of people use Six Sigma?
Six sigma is a common concept for people who have worked in statistics or operations research. Anybody involved in any aspect or business can benefit.
Because it requires a high degree of commitment, only leaders with strong leadership skills can implement it successfully.
What is Six Sigma?
It's an approach to quality improvement that emphasizes customer service and continuous learning. The goal is to eradicate defects through statistical techniques.
Motorola created Six Sigma as part of their efforts to improve manufacturing processes in 1986.
The idea quickly spread in the industry. Many organizations today use six-sigma methods to improve product design and production, delivery and customer service.
Six Sigma is so popular.
Six Sigma can be implemented quickly and produce impressive results. It can also be used to help companies identify and focus on the most important aspects of their business.
What is TQM exactly?
The industrial revolution was when companies realized that they couldn't compete on price alone. This is what sparked the quality movement. To remain competitive, they had to improve quality as well as efficiency.
In response to this need for improvement, management developed Total Quality Management (TQM), which focused on improving all aspects of an organization's performance. It included continual improvement processes, employee involvement, customer satisfaction, and customer satisfaction.
What is the difference between Six Sigma Six Sigma and TQM?
The major difference between the two tools for quality management is that six Sigma focuses on eliminating defect while total quality control (TQM), on improving processes and decreasing costs.
Six Sigma stands for continuous improvement. It emphasizes the elimination or minimization of defects through statistical methods such control charts and p charts.
This method seeks to decrease variation in product output. This is done by identifying root causes and rectifying them.
Total quality management involves measuring and monitoring all aspects of the organization. It also involves training employees to improve performance.
It is commonly used as a strategy for increasing productivity.
What is the best way to motivate your employees as a manager?
Motivation refers to the desire to perform well.
Doing something that is enjoyable can help you get motivated.
Another way to get motivated is to see yourself as a contributor to the success of the company.
If you are a doctor and want to be one, it will likely be more rewarding to see patients than to read medical books every day.
Motivation comes from within.
You may feel strongly that you are responsible to help others.
You might even enjoy the work.
If you don’t feel motivated, find out why.
Then think about how you can make your life more motivating.
Statistics
- The average salary for financial advisors in 2021 is around $60,000 per year, with the top 10% of the profession making more than $111,000 per year. (wgu.edu)
- This field is expected to grow about 7% by 2028, a bit faster than the national average for job growth. (wgu.edu)
- The BLS says that financial services jobs like banking are expected to grow 4% by 2030, about as fast as the national average. (wgu.edu)
- The profession is expected to grow 7% by 2028, a bit faster than the national average. (wgu.edu)
- Your choice in Step 5 may very likely be the same or similar to the alternative you placed at the top of your list at the end of Step 4. (umassd.edu)
External Links
How To
How can Lean Manufacturing be done?
Lean Manufacturing methods are used to reduce waste through structured processes. They were created by Toyota Motor Corporation in Japan in the 1980s. It was designed to produce high-quality products at lower prices while maintaining their quality. Lean manufacturing emphasizes removing unnecessary steps from the production process. It has five components: continuous improvement and pull systems; just-in time; continuous change; and kaizen (continuous innovation). Pull systems are able to produce exactly what the customer requires without extra work. Continuous improvement refers to continuously improving existing processes. Just-in-time refers to when components and materials are delivered directly to the point where they are needed. Kaizen stands for continuous improvement. Kaizen can be described as a process of making small improvements continuously. The 5S acronym stands for sort in order, shine standardize and maintain. These five elements are combined to give you the best possible results.
Lean Production System
Six key concepts underlie the lean production system.
-
Flow is about moving material and information as near as customers can.
-
Value stream mapping - break down each stage of a process into discrete tasks and create a flowchart of the entire process;
-
Five S’s - Sorted, In Order. Shine. Standardize. And Sustain.
-
Kanban is a visual system that uses visual cues like stickers, colored tape or stickers to keep track and monitor inventory.
-
Theory of constraints: identify bottlenecks in your process and eliminate them using lean tools, such as kanban board.
-
Just-in-time delivery - Deliver components and materials right to your point of use.
-
Continuous improvement - make incremental improvements to the process rather than overhauling it all at once.