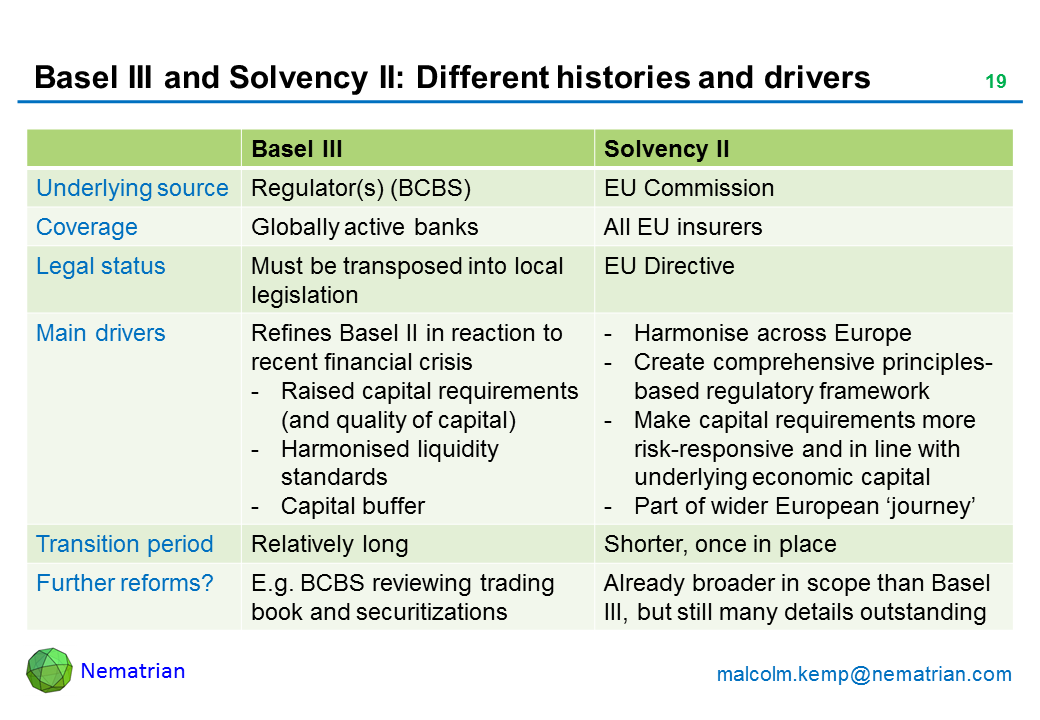
Before you can begin to work on a specific project, you must create a plan for project management. This document will define the process for obtaining resources, developing the resource management plan, and assigning roles for everyone. The plan should be discussed with your team. Include all stakeholders if you want your project to be completed on time. After you have created your plan, it's time to share it with your team.
The development of a project management strategy
It is essential to conduct basic assessments before developing a complete project management plan. This includes determining the expected project outcome as well as the due date. It is also important determine the weekly time commitment. It will be easier to reduce the amount of errors and time required for the project by creating a plan. In addition, this document will outline how the project will be delivered. Once these steps are completed, project managers can start to create a complete project management program.
The project scope statement forms an important part of the project manager plan. To avoid future ambiguity, it is essential to clearly define the scope of the project. It is crucial to identify any potential resources that may need to be used for the project. The document should also contain strategies for minimizing risks. It is crucial to include all deliverables, as well as their deadlines. It is crucial to include costs and the required resources.
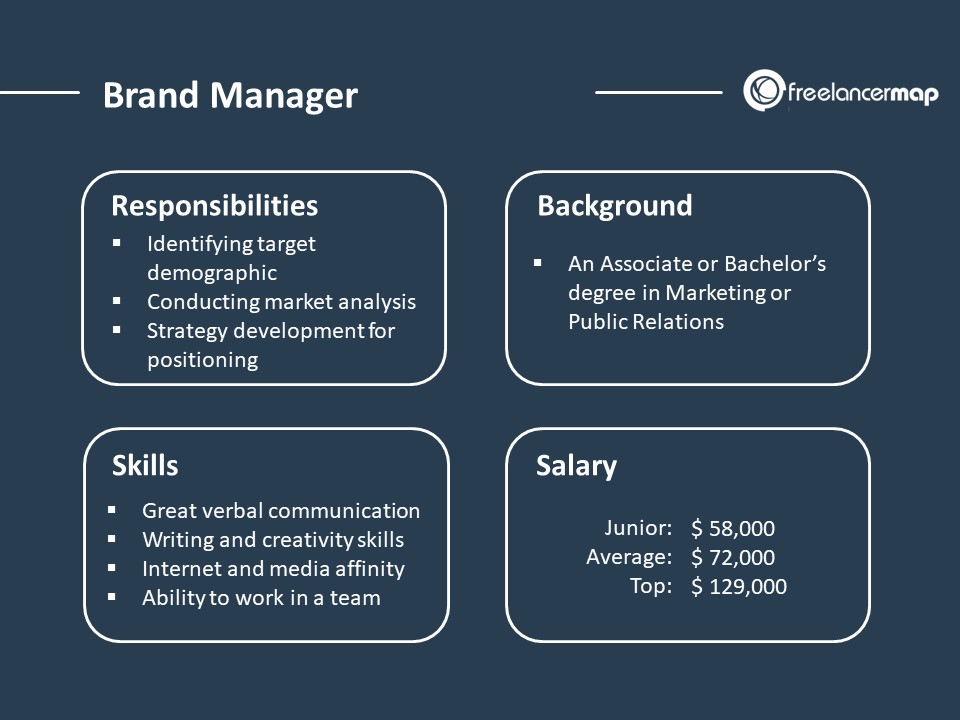
Identifying stakeholders
An important step in developing a project management program is to identify and communicate with stakeholders. Stakeholders can be individuals or groups that are affected in any way by a project. The project manager must determine the proper focus for each stakeholder. This could include customers, sponsors, employees or management. Each stakeholder can exert influence over the project deliverables. These are some methods that can be used to identify stakeholders.
First, identify those and organizations who have an interest. The second step in identifying stakeholders is to assess and determine each stakeholder’s influence and involvement. It is best to identify stakeholder early on in a project before it begins. Once identified, stakeholder can be categorized based on their influence and/or interest. This assessment should be done periodically throughout the project's lifetime.
Cost estimation
Developing a cost estimation is an important step in any project management plan. It acts as the base line for project expenses and allows for allocation of resources. A detailed description of the work required to create a cost estimate. Cost engineering is a practice of engineering that uses scientific principles and techniques to estimate and identify costs.
An accurate cost estimate should be based upon the best information available and on the experience of people involved in the project. Cost estimation should always be transparent, open and transparent. The cost estimate should be refined based on technical advice and engineering judgment. It should be based on all stakeholders' data, including customers and other stakeholders. It is important that the information used for estimating the cost of a project be accurate and in line with its scope.

Discussing the plan with your team
The first step in creating a project manager plan is to discuss it with your team. This will help ensure that everyone in the team understands the project management plan and what is expected. Assign tasks to team members. Clear directions and documentation are required to assign tasks. Before you start the project, ensure that everyone on your team has read the plan. For any questions on the project management plan, you can always reach out.
Make sure you discuss the project plan with everyone in your team. Don't forget to include everyone's input. You should use the plan as a starting line for discussion and not as a final product. Get feedback from both your client and your team. This will help you to make any necessary modifications to the plan.
FAQ
What does it mean to say "project management"
It refers to the management of activities related to a project.
Our services include the definition of the scope, identifying requirements, preparing a budget, organizing project teams, scheduling work, monitoring progress and evaluating the results before closing the project.
Why is it so important for companies that they use project management techniques
Project management techniques ensure that projects run smoothly while meeting deadlines.
This is due to the fact that most businesses rely heavily upon project work in order to produce goods, and services.
These projects must be managed efficiently and effectively by companies.
Without effective project management, companies may lose money, time, and reputation.
How can a manager enhance his/her leadership skills?
By practicing good management skills at all times.
Managers need to monitor their subordinates' performance.
You must quickly take action if your subordinate fails to perform.
It is essential to know what areas need to be improved and how to do it.
What are the four major functions of Management?
Management is responsible for organizing, managing, directing and controlling people, resources, and other activities. Management also involves setting goals and developing policies.
Organizations can achieve their goals through management. This includes leadership, coordination, control and motivation.
Management's four main functions are:
Planning - Planning refers to deciding what is needed.
Organizing is the act of deciding how things should go.
Direction - This is the art of getting people to follow your instructions.
Controlling - This is the ability to control people and ensure that they do their jobs according to plan.
What is TQM and how can it help you?
The industrial revolution led to the birth and growth of the quality movement. Manufacturing companies realized they couldn't compete solely on price. They needed to improve the quality and efficiency of their products if they were to be competitive.
Management responded to the need to improve, and developed Total Quality Management (TQM). This focused on improving every aspect of an organization’s performance. It included continual improvement processes, employee involvement, customer satisfaction, and customer satisfaction.
Statistics
- The profession is expected to grow 7% by 2028, a bit faster than the national average. (wgu.edu)
- 100% of the courses are offered online, and no campus visits are required — a big time-saver for you. (online.uc.edu)
- Our program is 100% engineered for your success. (online.uc.edu)
- Hire the top business lawyers and save up to 60% on legal fees (upcounsel.com)
- As of 2020, personal bankers or tellers make an average of $32,620 per year, according to the BLS. (wgu.edu)
External Links
How To
What is Lean Manufacturing?
Lean Manufacturing is a method to reduce waste and increase efficiency using structured methods. They were developed in Japan by Toyota Motor Corporation (in the 1980s). The main goal was to produce products at lower costs while maintaining quality. Lean manufacturing seeks to eliminate unnecessary steps and activities in the production process. It has five components: continuous improvement and pull systems; just-in time; continuous change; and kaizen (continuous innovation). Pull systems allow customers to get exactly what they want without having to do extra work. Continuous improvement is the continuous improvement of existing processes. Just-in-time is when components and other materials are delivered at their destination in a timely manner. Kaizen stands for continuous improvement. Kaizen can be described as a process of making small improvements continuously. Five-S stands for sort. It is also the acronym for shine, standardize (standardize), and sustain. These five elements are combined to give you the best possible results.
Lean Production System
Six key concepts underlie the lean production system.
-
Flow: The goal is to move material and information as close as possible from customers.
-
Value stream mapping: This is a way to break down each stage into separate tasks and create a flowchart for the entire process.
-
Five S's – Sort, Put In Order Shine, Standardize and Sustain
-
Kanban - visual cues such as stickers or colored tape can be used to track inventory.
-
Theory of constraints - identify bottlenecks during the process and eliminate them with lean tools like Kanban boards.
-
Just-in-time delivery - Deliver components and materials right to your point of use.
-
Continuous improvement is making incremental improvements to your process, rather than trying to overhaul it all at once.