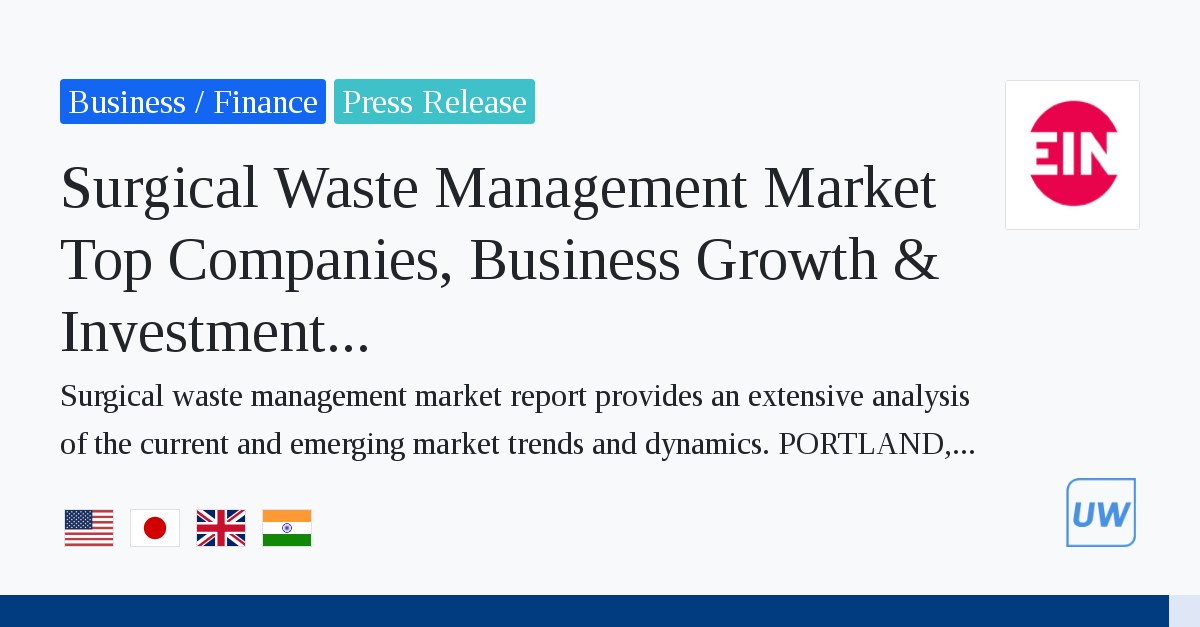
The self-managed definition can be challenging for a team, but it can also be advantageous to them. You will learn about the benefits and drawbacks of self-managed groups and how to implement them within your team. If you have read this article, then you will be able to make an informed decision as to whether self-managed team is right for your company. Continue reading if you aren’t convinced.
The disadvantages of self-managed teams
There are several advantages and disadvantages to using self-managed teams in your business. The structure provides more flexibility but can also create power vacuums in your team. While some people will assume leadership roles, others will be more comfortable with their responsibilities. Moreover, self-managed teams are not accountable to their management. It is difficult for managers to influence the team. This can lead to a decrease in productivity and creativity.
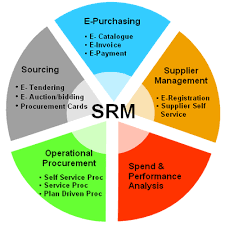
Self-managed organizations can have the disadvantage of being ineffective in enhancing organizational performance. To make these teams more effective, managers need to clarify their responsibilities and delegate authority. Also, it's possible for self-managed team members to fail in meeting their manager's goals. Therefore, self-managed teams should have a manager who holds the team accountable for results and provides coaching and feedback to team members.
Self-managed teams face challenges
Many benefits can be derived from self-managed teams. These teams tend to be more efficient than traditional teams, able to discuss ideas quickly and take action. These teams are more likely to be innovative as they assume responsibility for their own work. There are downsides, however. While self-managed team may be more appealing for some organisations, it's important to evaluate them before choosing them. Below we will look at some of the benefits and challenges of self-managed teams.
In addition to boosting team productivity, self-managed teams may also pose challenges to individual commitment. A lot of members in self-directed teams are specialists in one task. This can cause problems with collaboration and shared commitment. This problem can be alleviated by establishing a system in which team members can vote on a decision and agree on a course of action. Self-managed teams are less collaborative than traditional teams due to a lack of cross-team communication.
Methods to manage your own teams
To implement self-managed team, you must create a culture that encourages accountability. Instead of traditional teams where each member takes responsibility for their own decisions, self-managed groups are driven by the commitments made by all members. These commitments allow the work to move forward, as members acknowledge both their individual responsibilities and those of the group. This sense of accountability is reinforced throughout the team. This environment of accountability creates an environment that fosters creativity and innovation.
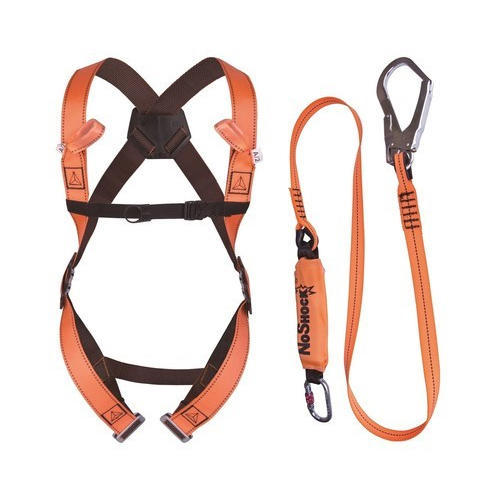
Setting clear goals and tasks is the first step to creating a self-managed group. The team can be given clear metrics to monitor its progress. For example, you might want to lead the industry in net promoter scores. In order to make sure the team succeeds, it may be necessary to hire new staff members if they are a new group. You may also want to train employees in self-managed groups to make sure they are aware of the changes.
FAQ
What are the steps of the management decision-making process?
Managers are faced with complex and multifaceted decisions. It includes many factors such as analysis, strategy planning, implementation and measurement. Evaluation, feedback and feedback are just some of the other factors.
It is important to remember that people are human beings, just like you. They make mistakes. As such, there are always opportunities for improvement, especially when you put in the effort to improve yourself.
This video will explain how decision-making works in Management. We discuss different types of decisions as well as why they are important and how managers can navigate them. The following topics will be covered:
How can we create a successful company culture?
A company culture that values and respects its employees is a successful one.
It's based on three main principles:
-
Everybody has something of value to share
-
People are treated fairly
-
There is mutual respect between individuals and groups
These values are reflected in the way people behave. They will treat others with respect and kindness.
They will respect other people's opinions.
And they will encourage others to share ideas and feelings.
A company culture encourages collaboration and communication.
People feel comfortable expressing their opinions freely without fear of reprisal.
They understand that errors will be tolerated as long they are corrected honestly.
The company culture encourages honesty and integrity.
Everyone is aware that truth must be told.
Everyone understands there are rules that they must follow.
Everyone does not expect to receive special treatment.
How do you define Six Sigma?
Six-sigma will be well-known to anyone who has worked in operations research or statistics. But anyone can benefit from it.
Because it requires a high degree of commitment, only leaders with strong leadership skills can implement it successfully.
What is the difference of leadership and management?
Leadership is about influencing others. Management is about controlling others.
Leaders inspire followers, while managers direct workers.
Leaders motivate people to succeed; managers keep workers on track.
A leader develops people; a manager manages people.
What's the difference between Six Sigma and TQM?
The key difference between the two quality management tools is that while six-sigma focuses its efforts on eliminating defects, total quality management (TQM), focuses more on improving processes and reducing cost.
Six Sigma stands for continuous improvement. It emphasizes the elimination and improvement of defects using statistical methods, such as control charts, P-charts and Pareto analysis.
This method attempts to reduce variations in product output. This is achieved by identifying and addressing the root causes of problems.
Total quality management is the measurement and monitoring of all aspects within an organization. This includes training employees to improve their performance.
It is commonly used as a strategy for increasing productivity.
What is the best way to motivate your employees as a manager?
Motivation refers to the desire to perform well.
You can get motivated by doing something enjoyable.
Another way to get motivated is to see yourself as a contributor to the success of the company.
For example, if you want to become a doctor, you'll probably find it more motivating to see patients than to study medicine books all day.
A different type of motivation comes directly from the inside.
For example, you might have a strong sense of responsibility to help others.
Maybe you like working hard.
Ask yourself why you feel so motivated.
Then think about how you can make your life more motivating.
Statistics
- The BLS says that financial services jobs like banking are expected to grow 4% by 2030, about as fast as the national average. (wgu.edu)
- Your choice in Step 5 may very likely be the same or similar to the alternative you placed at the top of your list at the end of Step 4. (umassd.edu)
- Our program is 100% engineered for your success. (online.uc.edu)
- This field is expected to grow about 7% by 2028, a bit faster than the national average for job growth. (wgu.edu)
- UpCounsel accepts only the top 5 percent of lawyers on its site. (upcounsel.com)
External Links
How To
How do you do the Kaizen method?
Kaizen means continuous improvement. The term was coined in the 1950s at Toyota Motor Corporation and refers to the Japanese philosophy emphasizing constant improvement through small incremental changes. It's a team effort to continuously improve processes.
Kaizen is one of Lean Manufacturing's most efficient methods. This concept requires employees to identify and solve problems during manufacturing before they become major issues. This will increase the quality and decrease the cost of the products.
Kaizen is a way to raise awareness about what's happening around you. So that there is no problem, you should immediately correct it if something goes wrong. Report any problem you see at work to your manager.
Kaizen follows a set of principles. Start with the end product, and then move to the beginning. In order to improve our factory's production, we must first fix the machines producing the final product. We then fix the machines producing components, and the machines producing raw materials. Finally, we repair the workers who are directly involved with these machines.
This method is known as kaizen because it focuses upon improving every aspect of the process step by step. Once we have finished fixing the factory, we return to the beginning and work until perfection.
Before you can implement kaizen into your business, it is necessary to learn how to measure its effectiveness. There are many methods to assess if kaizen works well. Another method is to see how many defects are found on the products. Another way is determining how much productivity increased after implementing kaizen.
You can also find out if kaizen works by asking yourself why you decided to implement it. Is it because the law required it or because you want to save money. Did you really believe that it would be a success factor?
Congratulations! You are ready to start kaizen.