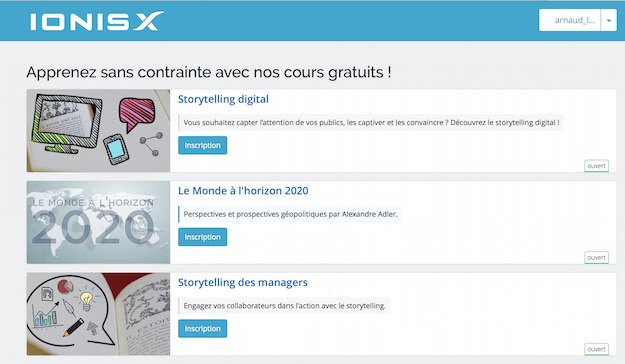
Finance risk management is the act of identifying, managing, and controlling risks for a business. This discipline is closely related to enterprise risk management. Investors in the money and those who originate structured products need it. This article will provide more information about finance risk management. Here are three reasons why this is crucial for your business.
Financial risk management involves assessing, evaluating, and controlling possible threats to a business.
Risk management can be found in every area of business. From the purchase U.S. Treasury bond to the use derivatives by fund manager to the approvals of personal lines by banks, it is everywhere. Stockbrokers use options, as well as other financial instruments, to hedge currency exposure. Money management strategies include asset allocation and portfolio diversification.
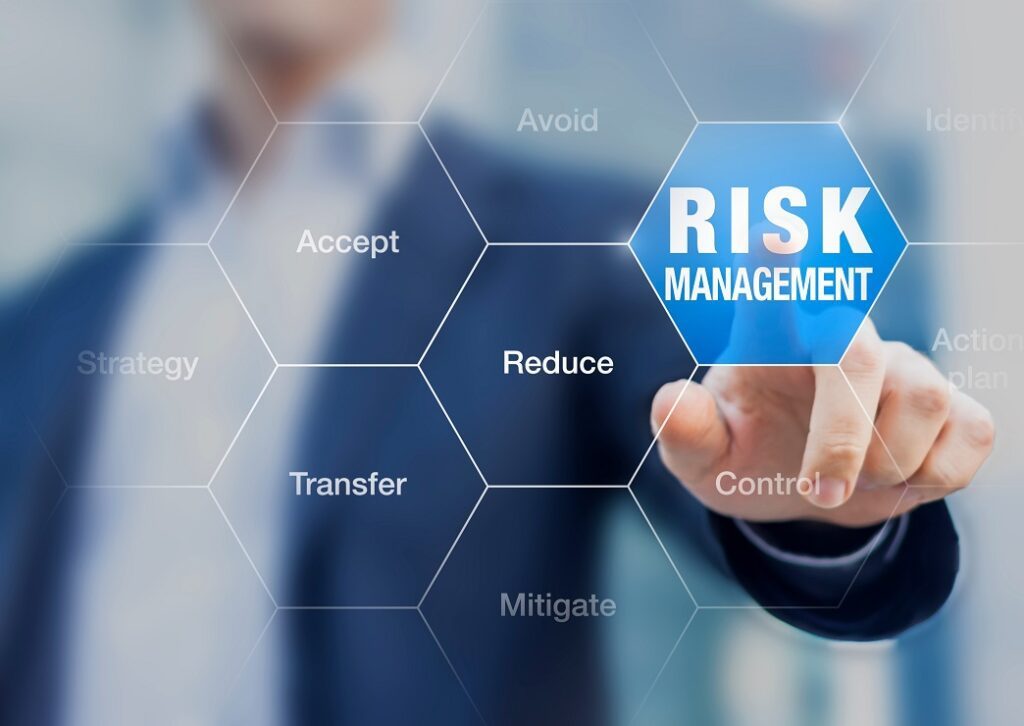
The first step of the process is to identify possible risks. These risks can be both internal and external to a business. For example, a financial risk might be caused by a technical malfunction or a legal liability. It could also be due to human error or natural disasters. A risk management program that is successful will take into account all possible risks and evaluate their impact on the company's strategic goals.
It is essential for investors in a money market
Money market investors need to be able to manage risk effectively. This requires an understanding of both the types of investments and the cash flows they generate. A good risk management strategy will balance the demand and supply of funds. Intangible assets should be considered by companies as part of their risk management strategies.
Many companies face different risks. These risks include credit, operational, and market risk. These risks are not as common for financial institutions than they are for non-financial companies. Financial institutions take credit and market risks deliberately, while nonfinancial entities take operational risk as a byproduct.
It is crucial for the originators of structured products
In today's environment, structured product originators need to be more careful about managing risk. To encourage them to do so, you can require them to retain a significant portion of the pool (including the senior and junior tranches). This would give them an incentive to use better risk management and build a more appealing portfolio.
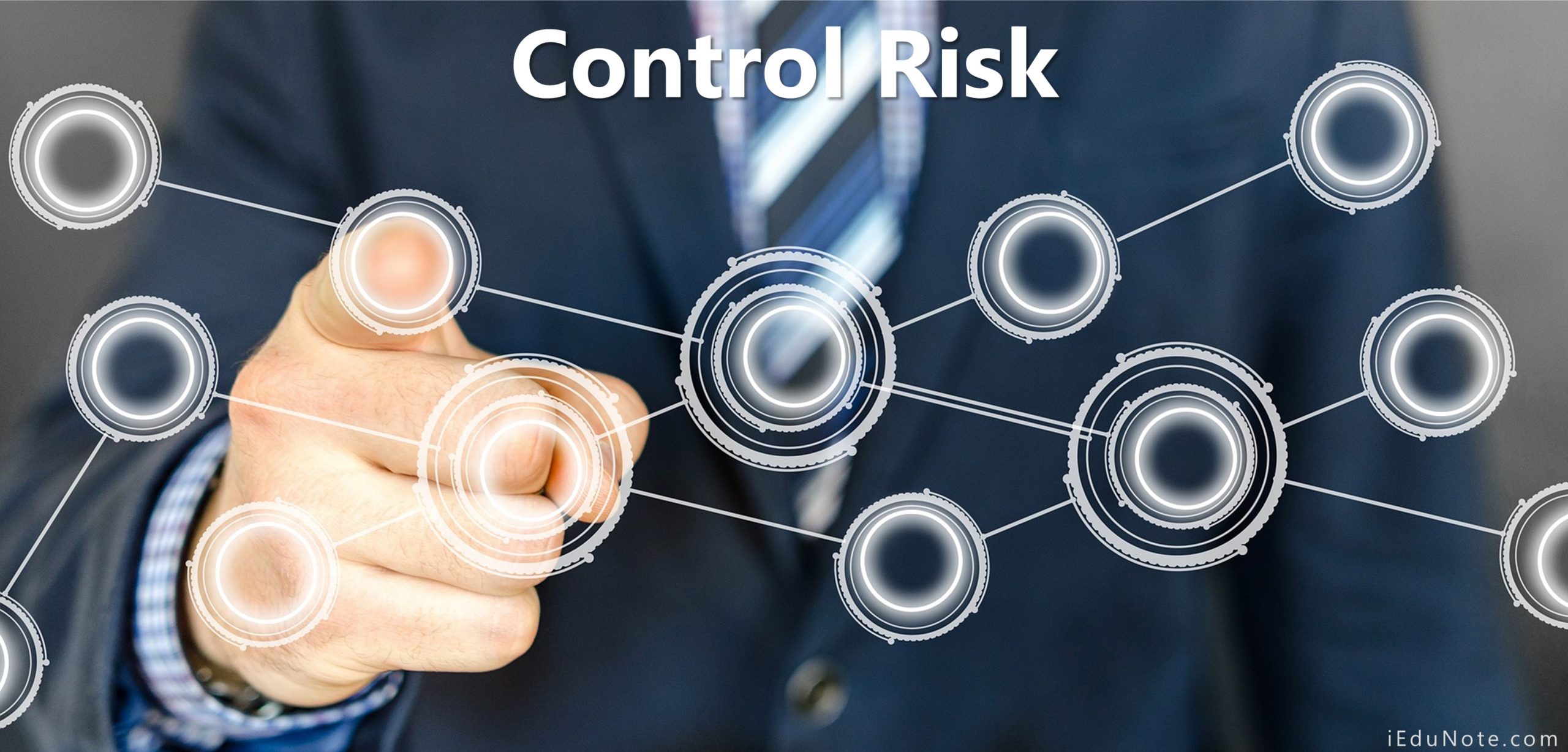
The financial crisis of 2008 is a clear example of why sound risk management is so important. Many people blame structured finance for the financial crisis, but the crisis was caused by poor risk management. Problems were not caused by the products; rather, they were due to the poor risk management of many financial institutions such as banks and mortgage brokers.
FAQ
What is the difference between leadership and management?
Leadership is about influencing others. Management is all about controlling others.
Leaders inspire others, managers direct them.
A leader inspires others to succeed, while a manager helps workers stay on task.
A leader develops people; a manager manages people.
What is the main difference between Six Sigma Six Sigma TQM and Six Sigma Six Sigma?
The main difference between these two quality-management tools is that six-sigma concentrates on eliminating defects while total QM (TQM), focuses upon improving processes and reducing expenses.
Six Sigma stands for continuous improvement. This approach emphasizes eliminating defects through statistical methods like control charts, Pareto analysis, and p-charts.
The goal of this method is to reduce variation in product output. This is done by identifying and correcting the root causes of problems.
Total Quality Management involves monitoring and measuring every aspect of the organization. It also involves training employees to improve performance.
It is used to increase productivity.
What is Kaizen and how can it help you?
Kaizen is a Japanese term meaning "continuous improvement." It is a philosophy that encourages employees to constantly look for ways to improve their work environment.
Kaizen is built on the belief that everyone should be able do their jobs well.
Statistics
- Your choice in Step 5 may very likely be the same or similar to the alternative you placed at the top of your list at the end of Step 4. (umassd.edu)
- This field is expected to grow about 7% by 2028, a bit faster than the national average for job growth. (wgu.edu)
- The BLS says that financial services jobs like banking are expected to grow 4% by 2030, about as fast as the national average. (wgu.edu)
- The profession is expected to grow 7% by 2028, a bit faster than the national average. (wgu.edu)
- 100% of the courses are offered online, and no campus visits are required — a big time-saver for you. (online.uc.edu)
External Links
How To
How does Lean Manufacturing work?
Lean Manufacturing techniques are used to reduce waste while increasing efficiency by using structured methods. They were created by Toyota Motor Corporation in Japan in the 1980s. The goal was to produce quality products at lower cost. Lean manufacturing seeks to eliminate unnecessary steps and activities in the production process. It includes five main elements: pull systems (continuous improvement), continuous improvement (just-in-time), kaizen (5S), and continuous change (continuous changes). Pull systems are able to produce exactly what the customer requires without extra work. Continuous improvement is constantly improving upon existing processes. Just-in time refers to components and materials being delivered right at the place they are needed. Kaizen means continuous improvement. Kaizen involves making small changes and improving continuously. Last but not least, 5S is for sort. To achieve the best results, these five elements must be used together.
Lean Production System
The lean production system is based on six key concepts:
-
Flow - The focus is on moving information and material as close as possible to customers.
-
Value stream mapping: This is a way to break down each stage into separate tasks and create a flowchart for the entire process.
-
Five S's, Sort, Set in Order, Shine. Standardize. and Sustain.
-
Kanban is a visual system that uses visual cues like stickers, colored tape or stickers to keep track and monitor inventory.
-
Theory of Constraints - Identify bottlenecks in the process, and eliminate them using lean tools such kanban boards.
-
Just-intime - Order components and materials at your location right on the spot.
-
Continuous improvement: Make incremental improvements to the process instead of overhauling it completely.