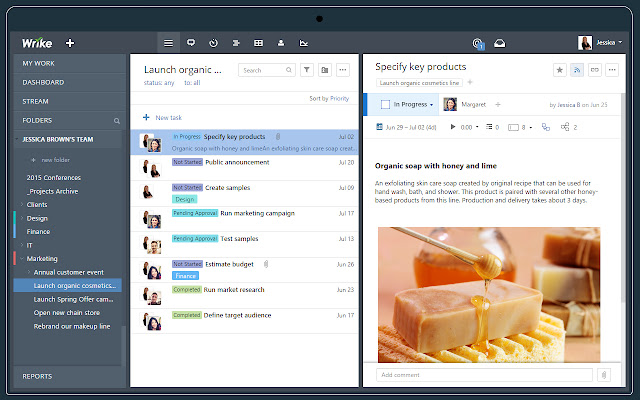
An important tool in project management is the RAID log. It can be used to help you understand your assumptions and identify risks. It can also assist you in managing issues and improving your project.
RAID logs can be used to communicate between project managers with stakeholders. It contains detailed information about decisions and activities taken during the project. This allows project managers and teams to keep track, make consistent decisions, and keep their team informed. RAID logs serve many purposes. By keeping a RAID log, you can monitor your project's progress, learn from past mistakes, and improve your next project.
RAID logs enable project managers identify risks and to assess their impact before making a decision on the course of action. These logs can be used to identify and resolve potential risks early on, or to assist you in understanding issues that may impact your project. This is an important step that you should take before the project starts.
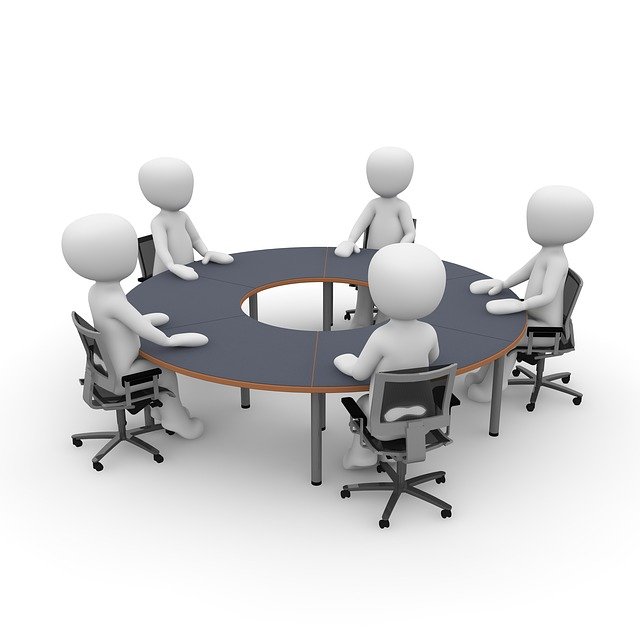
Projects cannot be avoided. They are often one of the most difficult aspects of a project to identify and manage. Failure to take the appropriate steps could lead to poor delivery and a project failure. It is crucial to identify and plan for mitigation of risks early in your project.
Risks can be divided into two categories: Low Impact items that have a minimal impact on the project and High Impact items which have a major negative impact. You can assess both the risk's likelihood and its severity to determine the impact. You can increase the probability of a risk being addressed if both are lower. Risks that are higher for either of these factors increase will be more severe. It is therefore important to regularly monitor the severity of risks.
Assumptions play a major role in projects. Even though you might not be able to prove a point, it is still a good idea to record your assumptions. You have many options to record your assumptions. The RAID log is one of the best places to start. Some Project/Program Directors prefer to be sole authors of the RAID log. Other managers prefer to use other tools such an issue log. It is important to document your assumptions formally, but they are often better used for long-term projects.
RAID logs can be used to evaluate risks and should be maintained throughout the project. It serves as a useful reference document, and can also be used for communication purposes. This is crucial for audits and status reporting. It is important to update the RAID log as soon as possible with new risks and/or details about existing issues. It's a great way to track your team's progress.
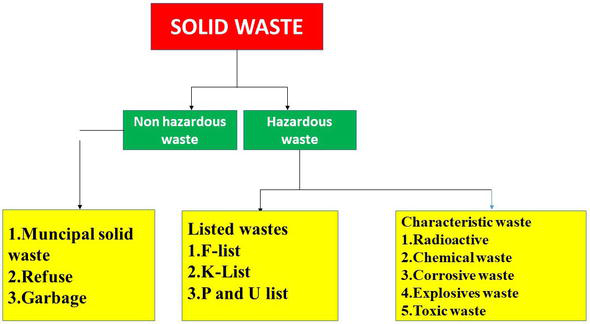
RAID logs are useful for project managers in the early stages. It can help you organize and keep all of your important information in one spot. RAID logs can also be used by you to collect data and to explain project issues, as well as track assumptions.
FAQ
What are some common management mistakes?
Managers sometimes make their own job harder than necessary.
They may not assign enough responsibilities to staff members and provide them with inadequate support.
In addition, many managers lack the communication skills required to motivate and lead their teams.
Managers sometimes set unrealistic expectations of their teams.
Managers may choose to solve every problem all by themselves, instead of delegating to others.
What is Kaizen?
Kaizen is a Japanese term which means "continuous improvement." This philosophy encourages employees to continually look for ways to improve the work environment.
Kaizen is a belief that everyone should have the ability to do their job well.
Why is it important for companies to use project management techniques?
Project management techniques ensure that projects run smoothly while meeting deadlines.
This is because many businesses depend heavily upon project work to produce products and services.
Companies must manage these projects effectively and efficiently.
Without effective project management, companies may lose money, time, and reputation.
What role should a manager play within a company
There are many roles that a manager can play in different industries.
Managers generally oversee the day-today operations of a business.
He/she makes sure that the company meets its financial obligations, and that it produces goods or services that customers desire.
He/she ensures employees adhere to all regulations and quality standards.
He/she plans and oversees marketing campaigns.
What is TQM?
When manufacturing companies realized that price was not enough to compete, the industrial revolution brought about the quality movement. They needed to improve the quality and efficiency of their products if they were to be competitive.
Management realized the need to improve and created Total Quality Management, which focused on improving all aspects within an organization's performance. It included continuous improvement and employee involvement as well as customer satisfaction.
Statistics
- Our program is 100% engineered for your success. (online.uc.edu)
- This field is expected to grow about 7% by 2028, a bit faster than the national average for job growth. (wgu.edu)
- The profession is expected to grow 7% by 2028, a bit faster than the national average. (wgu.edu)
- The average salary for financial advisors in 2021 is around $60,000 per year, with the top 10% of the profession making more than $111,000 per year. (wgu.edu)
- Your choice in Step 5 may very likely be the same or similar to the alternative you placed at the top of your list at the end of Step 4. (umassd.edu)
External Links
How To
How is Lean Manufacturing done?
Lean Manufacturing uses structured methods to reduce waste, increase efficiency and reduce waste. They were created in Japan by Toyota Motor Corporation during the 1980s. The goal was to produce quality products at lower cost. Lean manufacturing emphasizes removing unnecessary steps from the production process. It includes five main elements: pull systems (continuous improvement), continuous improvement (just-in-time), kaizen (5S), and continuous change (continuous changes). Pull systems allow customers to get exactly what they want without having to do extra work. Continuous improvement is the continuous improvement of existing processes. Just-intime refers the time components and materials arrive at the exact place where they are needed. Kaizen refers to continuous improvement. It is achieved through small changes that are made continuously. Five-S stands for sort. It is also the acronym for shine, standardize (standardize), and sustain. To achieve the best results, these five elements must be used together.
Lean Production System
Six key concepts form the foundation of the lean production system:
-
Flow - The focus is on moving information and material as close as possible to customers.
-
Value stream mapping - break down each stage of a process into discrete tasks and create a flowchart of the entire process;
-
Five S’s - Sorted, In Order. Shine. Standardize. And Sustain.
-
Kanban - use visual signals such as colored tape, stickers, or other visual cues to keep track of inventory;
-
Theory of constraints - identify bottlenecks in the process and eliminate them using lean tools like kanban boards;
-
Just-in Time - Send components and material directly to the point-of-use;
-
Continuous improvement - Make incremental improvements rather than overhauling the entire process.