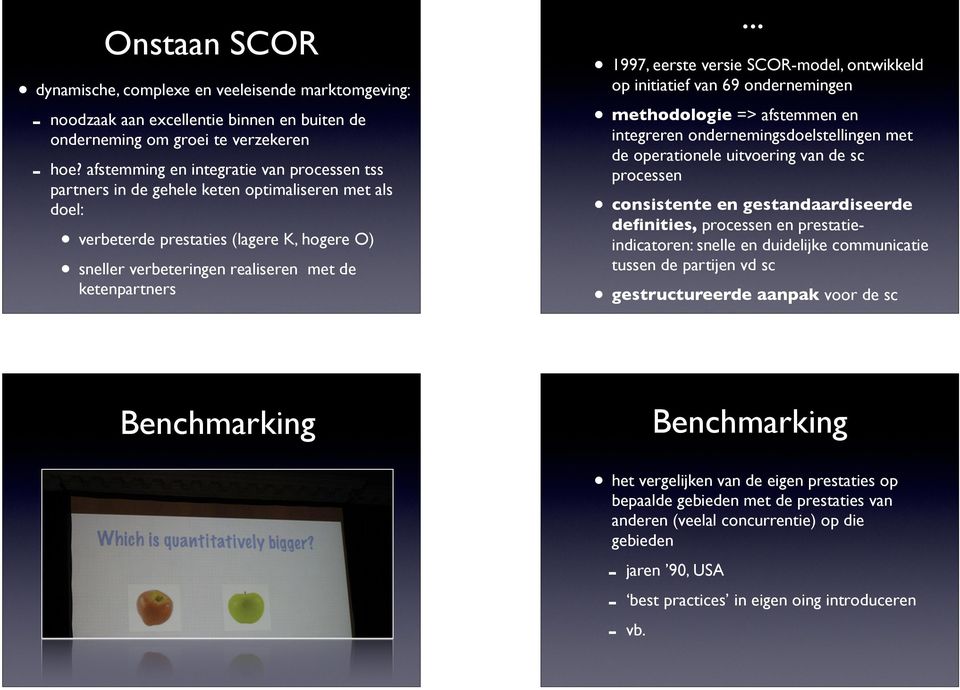
Multiple studies have been carried out to explore the dynamic of work flexibilty. They have focused on the different types of work flexibility, the relationship between flexible work and job satisfaction, and the impact of flexible working arrangements on the productivity and organizational performance. They have also assessed the impact of flexible working arrangements on the wellbeing of employees. They also looked at the benefits for both employees and employers.
These studies provide important insight into the effects of flexibility on employee performance. Flexible working arrangements are associated with higher job satisfaction and performance. Employees also have better control over their personal and professional lives. It was also discovered that employees working in flexible employment are more likely to develop preventive and psychosocial skills compared to employees with permanent job contracts.
This study also explores the impact of flexible working arrangements on the wellbeing and performance of employees, focusing on the four main types of work flexibility. These include working time flexibility and working space flexibility. This study examines the effects of different types of work flexibility on employee performance using a comparative analysis.
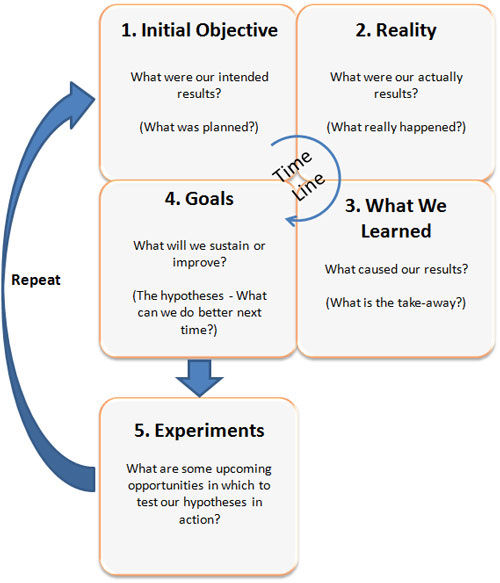
Flexible working arrangements also have an impact on employee wellbeing, productivity and organizational performance. This research has been conducted on the basis of the points of view of Romanian employees. To collect the views of employees, the study used the multiple correspondence analyze (MCA). MCA is a statistical technique that measures the magnitude of the explanation of variance in factorial scores. The MCA method differs to the PCA in that the dependent variable does not need to be observed. It assumes that the information is used in order to generate a composite indicator.
MCA approaches identify the first axis to be the ordering consistency principle that governs factorial scores. It is assumed that the factorial scores on the first axis will increase over time. Higher probabilities are found for this axis than for the threshold of 10% significance.
The main findings indicate that working time flexibility, functional flexibility, working space flexibility, and urgent management measures contribute most to the employee flexibility composite indicator. These three aspects are critical for job performance as well as job satisfaction.
The study provides a detailed analysis of the impact on job satisfaction, employee performance, and organizational performance of various types of work flexibility. This study also highlights how important new workspaces are for job performance as well as job satisfaction. The study revealed that new workspace types lead to improved organizational performance and job performances, as well increasing employee satisfaction and motivation.
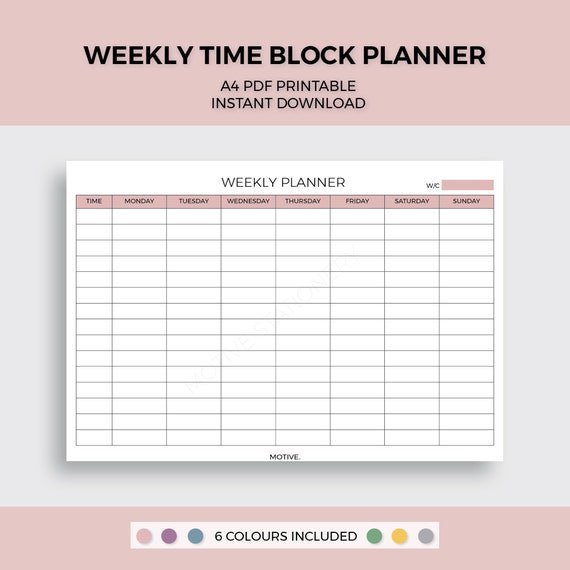
The authors used a comparative analysis to determine a positive correlation between work space flexibility, functional flexibility, and working time flexibility. A binary logistic regression model was used for determining the correlation. The Hosmer and Lemeshow tests have validated the model. This test indicates that the model is accurate in describing the data.
FAQ
What are the most important management skills?
Any business owner needs to be able to manage people, finances, resources and time. These skills include the ability of managing people, finances, time, space, and other factors.
Management Skills are also needed when you're setting goals and objectives, planning strategies, leading teams, motivating employees, resolving problems, creating policies and procedures, and managing change.
You can see that there are many managerial duties.
What is the difference in Six Sigma and TQM?
The main difference between these two quality-management tools is that six-sigma concentrates on eliminating defects while total QM (TQM), focuses upon improving processes and reducing expenses.
Six Sigma is a method for continuous improvement. This approach emphasizes eliminating defects through statistical methods like control charts, Pareto analysis, and p-charts.
This method seeks to decrease variation in product output. This is done by identifying and correcting the root causes of problems.
Total quality management is the measurement and monitoring of all aspects within an organization. It also includes the training of employees to improve performance.
It is often used as a strategy to increase productivity.
What is a simple management tool that aids in decision-making and decision making?
A decision matrix is a simple but powerful tool for helping managers make decisions. It helps them to think strategically about all options.
A decision matrix is a way to organize alternatives into rows and columns. This allows you to easily see how each choice affects others.
In this example, there are four possible options represented by boxes on the left-hand side of the matrix. Each box represents a different option. The status quo (the current condition) is shown in the top row, and what would happen if there was no change?
The effect of Option 1 can be seen in the middle column. In this example, it would lead to an increase in sales of between $2 million and $3 million.
The following columns illustrate the impact of Options 2 and 3. These are both positive changes that increase sales by $1million and $500,000. They also have negative consequences. Option 2 can increase costs by $100 million, while Option 3 can reduce profits by $200,000.
The last column shows you the results of Option 4. This means that sales will decrease by $1 million.
The best thing about a decision matrix is the fact that you don't have to remember which numbers go with what. It's easy to see the cells and instantly know if any one of them is better than another.
The matrix already does all the work. It is as simple a matter of comparing all the numbers in each cell.
Here is an example of how a decision matrix might be used in your business.
You want to decide whether or not to invest more money into advertising. If you do, you'll be able to increase your revenue by $5 thousand per month. However, this will mean that you'll have additional expenses of $10,000.
The net result of advertising investment can be calculated by looking at the cell below that reads "Advertising." It is 15 thousand. Advertising is a worthwhile investment because it has a higher return than the costs.
Statistics
- UpCounsel accepts only the top 5 percent of lawyers on its site. (upcounsel.com)
- The profession is expected to grow 7% by 2028, a bit faster than the national average. (wgu.edu)
- 100% of the courses are offered online, and no campus visits are required — a big time-saver for you. (online.uc.edu)
- This field is expected to grow about 7% by 2028, a bit faster than the national average for job growth. (wgu.edu)
- The average salary for financial advisors in 2021 is around $60,000 per year, with the top 10% of the profession making more than $111,000 per year. (wgu.edu)
External Links
How To
How does Lean Manufacturing work?
Lean Manufacturing techniques are used to reduce waste while increasing efficiency by using structured methods. These processes were created by Toyota Motor Corporation, Japan in the 1980s. The primary goal was to make products with lower costs and maintain high quality. Lean manufacturing emphasizes removing unnecessary steps from the production process. It is made up of five elements: continuous improvement, continuous improvement, just in-time, continuous change, and 5S. Pull systems allow customers to get exactly what they want without having to do extra work. Continuous improvement means continuously improving on existing processes. Just-in-time is when components and other materials are delivered at their destination in a timely manner. Kaizen refers to continuous improvement. It is achieved through small changes that are made continuously. The 5S acronym stands for sort in order, shine standardize and maintain. These five elements work together to produce the best results.
Lean Production System
Six key concepts underlie the lean production system.
-
Flow - The focus is on moving information and material as close as possible to customers.
-
Value stream mapping - Break down each stage in a process into distinct tasks and create an overview of the whole process.
-
Five S's, Sort, Set in Order, Shine. Standardize. and Sustain.
-
Kanban: Use visual signals such stickers, colored tape, or any other visual cues, to keep track your inventory.
-
Theory of constraints: identify bottlenecks in your process and eliminate them using lean tools, such as kanban board.
-
Just-in-time - deliver components and materials directly to the point of use;
-
Continuous improvement - incremental improvements are made to the process, not a complete overhaul.